Laboratory Roll Jar Mills/ Laboratory Ball Mills
These mills do the work rotating or spinning the mill jars for reduction in size in any condition or for the process of dispersion. What is Jar rolling mills. Laboratory jar rolling mills are electrically driven roller mechanisms for spinning or rotating milling jars, which are used for wet or dry size reduction, or dispersing.
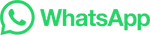