Specific surface area of particles by the Blaine and BET …
An effect of a grinding method, that is ball mill and high pressure grinding rolls (HPGR), on the particle size, specific surface area and particle shape of an iron ore concentrate was studied.
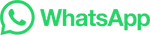