Ceramic ball wear prediction in tumbling mills as a grinding …
Traditionally, mill media wear rate is evaluated by measuring the media level in the mill, or by removing media charge and weighing it after a certain number of hours. As mentioned above, the mill was stopped after 24 h (one cycle) with a total of 24 cycles for each ceramic ball type. Grinding tests were carried out for 24 days (576 h) and ...
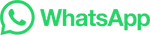