Ball Mill (Ball Mills Explained)
Ball mills are usually either of the grate (diaphragm) or overflow type. Ball Mill Components. Ball mills consist of the following components: Inlet – crushed ore is fed to the ball mill through the inlet. A scoop ensures the …
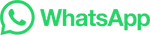