The Complete Guide to Primary Crushing, Secondary …
Working Principle of Secondary Crushers. The working principle of secondary crushers varies depending on the type of crusher, but generally, they work by applying pressure to the material through compression or impact. Cone crushers work by compressing the material between an eccentrically rotating mantle and a concave bowl.
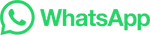