Numerical simulation study on rock-breaking process and mechanism …
The rock is broken into small cuttings, and an initial crushing pit is formed under the impact. The maximum principal stress of the rock is strongly tensile at the edge of the crushing pit, which easily forms tensile cracks and extends to the free surface of the rock, and further expands the rock crushing pit below the cutter.
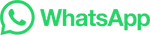