(PDF) SIZE REDUCTION BY CRUSHING …
gyratory crusher, with less steepness in the crush ing chamber and more of a parallel z one between . crushing zones. ... Working Principle of Impact Stone Cru sher .
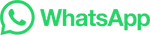
gyratory crusher, with less steepness in the crush ing chamber and more of a parallel z one between . crushing zones. ... Working Principle of Impact Stone Cru sher .
A gyratory crusher consists of a movable and truncated conical head and a fixed concave shell, as is presented in Figure 1. The head is integral with the main shaft, and it is covered by an element of wear named mantle. The set of these parts is the main shaft assembly.
Gyratory crushers work on the same principle as cone crushers (Figure 4.4(c)). These have a gyratory motion driven by an eccentric wheel. These machines will not accept materials with a large particle size and therefore only jaw or impact crushers should be considered …
The working principle of primary crushers varies depending on the type of crusher, but generally, they work by reducing the size of the material through compression or impact. In jaw crushers, the …
Working Principle of Crushers. On left is a showing of the "standard gyratory with straight concaves" is a section through any vertical, radial plane in the crushing chamber of one of the intermediate sizes of the crusher. In order to understand the crushing action in such a chamber it is helpful to consider the process as though each step took place in an …
2. GYRATORY CRUSHERS. The original patent for the gyratory crusher was granted to Phile- tus W. Gates in 1881. This fint crusher was used by the Buffalo Cement Co. At the …
The single-toggle jaw crusher with the largest antifriction bearings and highest flywheel energy 1) with new crushing elements 2) 1,200 r.p.m. possible ... Schematic diagram of the working principle of a single-toggle jaw crusher with a single-toggle system Left: Single-toggle jaw crusher with main components Crusher
Cone crusher and gyratory crusher work on the same principle. Both have the same operation. If cone crusher differs then it is only from crushing chamber. Cone crusher has a less steep crushing chamber and more parallel zone between crushing zones. It breaks the rocks by squeezing it between the gyrating spindles.
Gyratory crushers are always installed vertically orientated. A gyratory crusher's size is classified by: Its gape and mantle diameter. The diameter of the receiving opening. …
The Gyratory Crusher TS is distinguished from other gyratory crushers by its revolutionary design which allows you to easily and safely perform major service and maintenance functions. It is designed so that you can easily access and remove the eccentric assembly, bushings and hydraulic piston through the top of the crusher, hence the name ...
A sectional view of the single-toggle type of jaw crusher is shown below. In one respect, the working principle and application of this machine are similar: the movable jaw has its maximum movement at the …
Gyratory Crusher's Working Principle. The gyratory crusher operates on a gyratory motion principle, which means it works by rotating a mantle within a concave bowl. As materials enter the crusher, they are crushed between the mantle and the concave bowl, resulting in a reduction in size. The crushing action is continuous, …
May 2015. Magnus Evertsson. PhD Thesis Cone crushers are used by both the aggregate producing and the mining industry. Both industries are interested in increasing the product quality while at the ...
GYRATORY CRUSHERS. The original patent for the gyratory crusher was granted to Phile- tus W. Gates in 1881. This fint crusher was used by the Buffalo Cement Co. At the time these early gyratory crushers were developed all mining and quarrying, either underground or open pit, was done by hand; tonnages generally were small and product ...
Gyratory crusher is a crushing equipment that uses the gyratory motion of the crushing cone in the conical cavity inside the shell to extrude, bend, and impact …
1) Working Principle. Two interface cones form a crushing cavity that gets smaller downwards. The shell is called a fixed cone. The moving cone is suspended on a beam over the top of the fixed cone. When the crusher moves downward, it is eccentric. When the shaft sleeve rotates, the moving cone and the conical surface are eccentrically …
Essentially, a gyratory crusher consists of a heavy cast-iron, or steel, shell/frame which includes in its lower part an actuating mechanism (eccentric and driving gears), and in its upper part a cone shaped crushing chamber, lined with wear resisting plates (concaves). Construction detail and working of the crusher is as under. The main shaft ...
The working process of the gyratory crusher is used as a specific analytical target in this paper, and the performances of the gyratory crusher, including productivity, mass percentage of effective particles, and crushing force, are explored through DEM simulation. ... Gyratory crusher principle. The gyratory crusher is mainly composed of …
The cone crusher has a high reduction ratio, ensuring efficient material crushing. Discharge: This is the final stage of the crushing process. When the material is crushed into the preferred size, it exits the cone crusher through an opening at the bottom. The entrance is located between the mantle and the bowl liner.
2. Both the structure and working of a jaw crusher are quite simple. 3. The product size is quite small and can range up to millimetres. 4. Repair and maintenance of a jaw crusher are convenient and easy. 5. The reliability of a jaw crusher is significantly high. 6. The broken parts of the jaw crusher are easy to replace. Disadvantages of a Jaw ...
To work a gyratory crusher, you will need to adjust the size of the opening at the bottom of the crusher to allow for the right sized rocks to enter. You will then need to turn on the machine and ...
The secondary crushers are also designed on the principle of gyratory crushing, but the construction details vary. ... A long shaft suspended spindle gyratory crusher 12.7 cm × 127 cm was commissioned to crush limestone with a work index of 13.2 kWh/t. The crusher was adjusted to a throw of 0.7 cm and the set at 2.54 cm. The …
Essentially, a gyratory crusher consists of a heavy cast-iron, or steel, shell/frame which includes in its lower part an actuating mechanism (eccentric and driving gears), and in its upper part a cone shaped crushing chamber, lined with wear resisting plates (concaves). Construction detail and working of the crusher is as under. The main shaft ...
How Gyratory Crushers Work Gyratory crushers may seem like complex machines, but their principle of operation is surprisingly straightforward. At its core, a gyratory crusher consists of a mantle that rotates within a concave bowl-shaped housing.
Cone crushers and jaw crushers both work by compression, reducing materials by squeezing them until they break apart. The benefit that cone crushers offer over jaw crushers is their ability to output a more cubical product similar to impact crushers. Cone crushers have traditionally been used as secondary and sometimes tertiary crushing ...
Impact Crusher Working Principle. Starting from the base working principle that compression is the forcing of two surfaces towards one another to crush the material caught between them. Impact crushing can be of two variations: gravity and dynamic. An example of gravity impact would be dropping a rock onto a steel plate …
The Working Principle Of Gyratory Crusher – Austin Matzko's …. The working principle of gyratory crusher There are numerous distinct forms of, stone crushing production line are usually utilised, total production line and ….
Gyratory crusher is a crushing equipment that uses the gyratory motion of the crushing cone in the conical cavity inside the shell to extrude, bend, and impact materials, for the purpose of coarse crushing of the materials of various hardness. It was invented in the USA in the 1870s. The equipment specification is usually represented by …
Gyratory crushers – design and operating principle Technical data Design A Spider bearing in two-armed spider ensures spacious feed opening, automatic lubrication …
In terms of design and construction, gyratory crushers and cone crushers have distinct differences. A gyratory crusher has a mantle that rotates within a concave bowl, while a cone crusher has a mantle that rotates within a bowl-shaped concave. This design allows for a larger feed size and a higher capacity for both types of crushers, but ...
حقوق النشر © 2024.Artom كل الحقوق محفوظة.خريطة الموقع