Predicting the Overall Specific Energy Requirements of …
conventional ball mills (fine particles) it is labelled M ib. For HPGRs it is labelled M ih Wi = Specific comminution energy at pinion (kWh/tonne) x2 = 80% passing size for the product (microns)
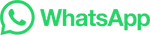