Simulation of wet ball milling of iron ore at Carajas, Brazil
The tests were made in a steel cylindrical ball mill of 250 mm internal diameter (D T) and 250 mm length (L T) fitted with eight symmetrically located horizontal lifters (see Table 1) and smooth end walls, with one end wall removable and locked in place with a quick release locking clamp.The media were stainless steel ball bearings of 25.4 …
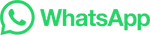