Comminution and classification technologies of iron ore
Ball mills are filled up to 40% with steel balls (with 30–80 mm diameter) which effectively grind the ore. The material to be ground fills the voids between the balls. The tumbling balls capture the particles in ball/ball or ball/liner events and load them to the point of fracture. ... HPGR application at Karara iron ore mine—adopted ...
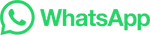