material flow inside vertical roller mill design
Now many large vertical roller mill machine manufacturers are some of the machinebuilding technology at home and abroad, based on years of experience and customer demand for the design and development of a new type of grinding equipment, such equipment the original grinding process The steps of the integration, first of all …
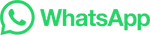