Full article: Evaluation of optimization techniques for …
The cement raw mill is the primary piece of equipment used in the modern cement industry for the raw meal production process. As a result, it is critical to …
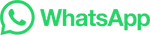
The cement raw mill is the primary piece of equipment used in the modern cement industry for the raw meal production process. As a result, it is critical to …
Typical 3DCP process uses natural river sand and ordinary Portland cement (OPC) as prime raw material. 5–8 The production of OPC alone accounts for 5% of global anthropogenic CO 2 emissions, 9 and the increasing demand for river sand also leads to overexploitation of such resources and potential negative environmental impacts. 10 …
The fly ash processing plant constructed by AGICO Cement is highly automated and mechanized, with low investment, high profit, simple structure and easy operation, which helps each region realize reasonable waste recycling and utilization to 'green up' users' supply chains. Raw Material.
Cement is widely used in emerging industries and engineering construction, such as industrial construction, civil construction, transportation engineering, hydraulic engineering, seaport engineering, and national defense construction (Zhao et al. 2022).The cement raw material is obtained by mixing and grinding calcium material, siliceous …
Cement Additives. Cement additives are materials added to cement for the optimization of the cement properties and the cement grinding process. Cement additives are classified into different product groups such as …
The cement production process 1. The Quarry: The cement production process begins with the extraction of limestone and clay from the quarry. 2. Crusher and Pre-Blending: The material is then crushed to reduce particle sizes and blended to reduce variability in composition. 3. Raw Mill and Kiln: Raw materials and additives are
Concrete is formed when portland cement creates a paste with water that binds with sand and rock to harden. Cement is manufactured through a closely controlled chemical combination of calcium, silicon, aluminum, …
The production of clinker in a kiln is a key process in the production of cement. The raw materials used in this process typically include limestone, clay, and sands while other minerals such as iron ore and shale can also be used. ... Both types of mills are commonly used in the production of cement. Once the clinker and additives have been ...
The primary raw materials of dry concrete are essentially the same as those of conventional concrete. The following sections elaborate the raw materials including the cementitious components, aggregate and additional additives (chemical addition and fibre) of dry concrete in detail. 2.1.1. Cementitious material
Additives (like sand and iron ore), along with the limestone and clay, are fed from bins to the raw mill. An extremely important step in the cement process is to proportionally feed …
There are three steps of the high-temperature system: Drying or preheating, calcining, and sintering. The calcining is the core part of the clinker production; the raw meal is weighed and sent into preheater and cement kiln to process clinker. Grate cooler helps to cooler clinker, the cooled clinker is sent to the cement silo for storage.
The principal goal of raw material design and preparation is a kiln feed that permits effective, energy-conserving production of a quality portland cement clinker. Such clinker must have very restricted compositional targets. Since clinker must contain substantial portions of the elements calcium, silicon, aluminum, and iron, the raw materials ...
CHRYSO ® Reductis 50 reduces significantly the Hexavalent Chromium content in cement even at low dosages. It allows to maintain durably the Chromium VI content below 2 ppm to be in line with the 2003/53/CE European standards. Limited installation and maintenace costs. CHRYSO ® Reductis 50 is a liquid solution easy to introduce through a ...
two separate Cement Production lines can be summarized into the following processes ;as can be seen in the process and Quality flow diagram below; 1. Quarrying and Crushing 2. Raw material Storage and Transportation 3. Proportioning 4. Raw material Grinding and Transportation 5. Raw meal storage, homogenization and Kiln feeding 6.
You've already forked sbm 0 Code Issues Pull Requests Packages Projects Releases Wiki Activity
How Concrete is Made: Aggregates. Aggregates, which make up roughly 60% to 75% of ready-mix concrete's volume, are obtained from quarries and aggregate banks. How Concrete is Made: Additives. Additives are solid or liquid chemical substances that can be added to ready-mix concrete before or during preparation. Most commonly used …
Cement additives. Product performance depends, to a large extent, on raw materials, grinding equipment, and process parameters. BASF, a leading chemical company, is offering an innovative range of grinding aids and performance enhancers for the needs of cement industry. These additives are offered under the brand Cementium.
Cement mill is another necessary cement equipment of the cement plant. After raw material crushing, cement mill plays vital role in the further cement manufacturing process. Cement ball mill, vertical cement mill, and cement roller press are common types of cement grinding plant. cement ball mill. Cement mill has two functions of the cement ...
Assessing the environmental impact of conventional and 'green' cement production. G. Habert, in Eco-efficient Construction and Building Materials, 2014 10.1 Introduction. Cement production has undergone tremendous developments since its beginnings some 2,000 years ago. While the use of cement in concrete has a very long history …
Raw materials chemistry. Cement manufacture requires a source of calcium, such as CaCO 3 or CaMg (CO 3) 2, which comprises almost 80–90% of the total and the rest is iron oxide (Fe 2 O 3, Fe 3 O 4), quartz (SiO 2), and clay/bauxite (Al-silicates) (Aïtcin and Flatt Citation 2015; Hewlett Citation 2003; Peray and Waddell Citation …
Providing a comprehensive guide to the entire cement production process from raw material extraction to the finished product, the industry's favourite technical reference book is now fully ... Typical equipment downtime 110 1. Storage of clinker and other components – 2. Cement milling – 3. Separators (classifiers) – 4. Ball mill circuit
Generally, the proportion of components in cement raw materials is 67-75% limestone, 10-15% clay, 0.5-1.5% iron ore and 8.5-11% coal. The laboratory of a cement plant. With the help of vertical roller mills or other types of crushers, the raw materials are blended and further ground into smaller pieces of raw meal in the cement plant.
The quality of cement clinker is directly related to the chemistry of the raw materials used. Around 80–90% of raw material for the kiln feed is limestone. Clayey raw material accounts for between 10–15%, although the precise amounts will vary. Magnesium carbonate, which may be present in limestone, is the main undesirable impurity. The level
cement, in general, adhesive substances of all kinds, but, in a narrower sense, the binding materials used in building and civil engineering construction. Cements of this kind are finely ground powders that, when mixed with water, set to a hard mass. Setting and hardening result from hydration, which is a chemical combination of the cement ...
Admixtures are artificial or natural materials added to the concrete besides cement, water and aggregate to improve certain property of concrete during casting or setting or service stage. A material other than water, aggregates, or cement that is used as an ingredient of concrete or mortar to control setting and early hardening, workability ...
06.29.22. Sika i s bringing a new manufacturing plant for concrete admixtures on stream in Stafford, ia. With the opening of the plant near Washington D.C., Sika is increasing its production capacity in the important American construction market so that it can readily satisfy the strong demand in the Northeast and Mid-Atlantic regions.
The composition of raw materials, additives, and fuel has a significant bearing on cement's properties. Limestone used for cement production by different …
A 2 500 t/d cement production line can adopt roller mill as the main raw material grinding machine. Under normal conditions, it will be equipped with the static powder separator (air volume 350 000-450 000 m/h) and …
Schenck Process provides cement processing equipment. Discover our range of high quality machines and rely on 135 years of experience.
Additive Manufacturing (AM) with concrete, also known as 3-D Concrete (3DCP), is an emerging technology in the construction industry. This approach to …
حقوق النشر © 2024.Artom كل الحقوق محفوظة.خريطة الموقع