Removal of Cr(VI) from aqueous solution using ball mill …
Preparation of BM-WB: 10 g WB and 100 g agate balls (8, 10, 15 mm in diameter) were mixed into agate bottles, and then the agate bottles were placed in a planetary ball mill (MITR-YXQM-2L ...
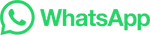