BALL MILLS Ball mill optimisation
ground by an unadjusted ball charge and as a result, mill performance is yet again reduced. As shown in Figure 1, all these small, interlinked process steps need to be …
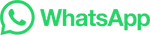
ground by an unadjusted ball charge and as a result, mill performance is yet again reduced. As shown in Figure 1, all these small, interlinked process steps need to be …
A) Total Apparent Volumetric Charge Filling – including balls and excess slurry on top of the ball charge, plus the interstitial voids in between the balls – expressed as a percentage of the net internal mill …
With the installation of one or both of these machines between the ball mill and classifier, as high as 70 per cent of the free gold and sulphide minerals can be immediately removed, thus reducing grinding costs and improving over-all recovery. ... Rubber lining, grate mill. Ball Mill Charge volume. The mill power is approximately …
The working ball charge in the mill will be as shown in Table 12. Working Ball Charge in Ball Mill. Suppose that once every week the mills are stopped and all balls less than 2 in. in diameter are removed. If the ball wear is 2 lb. per ton of ore crushed, this will amount to 720 lb. (326.5 kg.) per day for each mill.
For overflow ball mills, the charge should not exceed 45% of the mill volume . For grate discharge mills, the charge should occupy about 50% of the mill volume . Bond developed a relationship that can be used to …
These mills typically grind ROM ore in a single stage. A large example of such a mill was converted from a single-stage milling application to a semi autogenous ball-mill-crushing circuit, and the application is well described. This refers to high-aspect AG/SAG mills. Ball Charge Motion inside a SAG Mill. With a higher density mill charge.
The charge of grinding media for two-compartment ball mill can be calculated for dry grinding of cement raw mix. The medium-hard raw material for the mill feed has a particle size range of 0.5 to 25 mm. The mill dimensions are: -. Inner diameter of mill = 4.2 m. Length of drum = 15.25–1.0 = 14.25 m.
with Patented Ball Feeding Indexer. The Auto Ball Charging system was developed to make the loading of balls into a Ball Mill safer and easier. …
Crushed ore is fed to the ball mill through the inlet; a scoop (small screw conveyor) ensures the feed is constant. For both wet and dry ball mills, the ball mill is charged to approximately 33% with balls (range 30-45%). …
The Planetary Ball Mill PM 200 is a powerful benchtop model with 2 grinding stations for grinding jars with a nominal volume of 12 ml to 125 ml. The extremely high centrifugal forces of Planetary Ball Mills result in very high pulverization energy and therefore short grinding times. The PM 200 can be found in virtually all industries where the ...
Small Ball Mill Capacity & Sizing Table Ball Mill Design/Power Calculation
The ball charge of a SAG mill is about 29% to 30%. By friction and influence of tumbling balls inside rotating cylinder grinds the raw material to the required fineness. The internal machinery of ball mill grinds the raw material into the powder-like material, And if extreme fineness and refinery are required then rotation go on continue.
A ball mill also known as pebble mill or tumbling mill is a milling machine that consists of a hallow cylinder containing balls; mounted on a metallic frame such that it can be rotated along its longitudinal axis. The balls which could be of different diameter occupy 30 – 50 % of the mill volume and its size depends on the feed and mill size.
A ball mill consists of various components that work together to facilitate grinding operations. The key parts include the following: Mill Shell: The cylindrical shell provides a protective and structural enclosure for the mill. It is often made of steel and lined with wear-resistant materials to prolong its lifespan.
Planetary Mills are ideally suited for fine grinding of hard, medium-hard, soft, brittle, tough and moist materials. The comminution of the material to be ground takes place primarily through the high-energy impact of grinding balls in rotating grinding bowls. The grinding can be performed dry, in suspension or in inert gas.
Ball charge Mixer Mills MM 200 / MM 400 / MM 500 vario / CryoMill The MM 400 and the CryoMill (at room temperature) are suitable for wet grinding. For optimal wet grinding …
The approximate horsepower HP of a mill can be calculated from the following equation: HP = (W) (C) (Sin a) (2π) (N)/ 33000. where: W = weight of charge. C = distance of centre of gravity or charge from centre of mill in feet. a = dynamic angle of repose of the charge. N = mill speed in RPM. HP = A x B x C x L. Where.
Ball size and ball grade is determined by the feed ore size and hardness, plus the PH level of the slurry. The ball charge is determined by the operator targeting the balance …
incl. order data. Download. The Planetary Ball Mill PM 100 is a powerful benchtop model with a single grinding station and an easy-to-use counterweight which compensates masses up to 8 kg. It allows for …
Each ball feeder/counter system is designed to accept a narrow range of ball diameters and should not be used to charge balls of mixed sizes. Weight-based counter The AutoCharge system's weight-based counter is suitable for all ball diameters but is particularly applicable to smaller ball sizes (50–80 mm), including ball recharge practice ...
Ball mill machines are essential equipment for processing powder materials in various industries, including the food, pharmaceutical, and chemical industries. A ball mill machine is used to grind and mix materials, producing a finely ground powder suitable for a wide range of applications. ... Ball Charge: The ball charge is the total number of ...
Mining Area. Links and Contact. - Ball charges: This calculator gives the surface and the average weight of the ball charges. It gives also a rough interpretation of the ball charge efficiency: - Ball top size (bond formula): calculation of the top size grinding media (balls or cylpebs): - Modification of the Ball Charge: This calculator ...
Particle size reduction of materials in a ball mill with the presence of metallic balls or other media dates back to the late 1800's. The basic construction of a ball mill is a cylindrical container with journals at its axis. The cylinder is filled with grinding media (ceramic or metallic balls or rods), the product to be ground is added and ...
The production of fines is low and consequently a rod mill is the right machine when a steep particle size distribution curve is desired. A product with 80% minus 500 microns can be obtained in an economical manner. ... particles pass a screen with 25 x 25 mm apertures shall be ground to approx. 95% passing 0.1 mm in a 2.9 x 3.2 m ball …
The better mills on the market have an efficiency of about 8-9 % which means that only 8-9 % of the energy results in grinding and the majority is converted mainly into heat. The ball mill has the worst efficiency of all types of mills on the market. Just 4 % of the energy is used for comminution. Nevertheless when grinding is required the ball ...
Here we list 17 signs to mention you that the ball mill is running and needs to be checked in. Find the abnormal signs early is very important to prolong the ball mill service life. 1. The sign of "swollen belly". Just like a bloated stomach, if the amount of grinding exceeds the maximum capacity and discharge capacity, it will cause the mill ...
The ball mill is equipped with a classifying lining with a conical undulated shape. The absolute lifting height is quite similar to an industrial used liner plate. The discharge diaphragm is of the slotted type. The ball charge grading used during most of the test runs was an industrial standard grading with balls between 12 and 20 mm.
Fig. 1 shows typical charge shapes predicted for our 'standard' 5 m ball mill and charge (described above) filled to 40% (by volume) for four rotation rates that span the typical range of operational speeds. For such a charge with a realistic size range, the free surface of the charge is well defined at low and intermediate rotation rates. For N=60%, …
Fast & Powerful. Loss-free size reduction down to the submicron range. Wet grinding yields particle sizes in the nanometer range (<100 nm) Variable speed from 50 to 800 rpm, …
Abstract. Discrete element method (DEM) modelling has been used to systematically study the effects of changes in mill operating parameters and particle …
حقوق النشر © 2024.Artom كل الحقوق محفوظة.خريطة الموقع