Effect of ball mill grinding parameters of hydrated lime …
In this matter, the objective of this paper is to investigate the ef-fect of the various grinding parameters such as ball charge filling ratio, material charged ratio, and mill speed on the properties of hydrated lime and fineness of the product using a ball mill. product. Limestone or calcium carbonate (CaCO3) exists as a natural stone in nature.
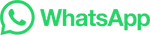