(PDF) NaOH-assisted direct reduction of Ring of Fire chromite ores…
In the deposition of metallic phase within the complex oxide, there is no direct contact between the metal and reducing agent; therefore, in the reduction of iron in complex or lean ores by carbon ...
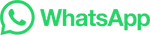