Primary Crushing: A Comprehensive Guide
These bits are often between 150 and 200 mm. This step is very important. It makes the rocks smaller. This helps the next machines work better at crushing or …
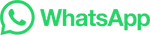
These bits are often between 150 and 200 mm. This step is very important. It makes the rocks smaller. This helps the next machines work better at crushing or …
There are two kinds of. equipments used for crushing work s. one is by using crushers and other one is by using impacto rs. This diagram illustrates the stages of s ize reduction from 1000mm to 4 ...
It may often look like sand, though it is actually part of the process of crushing limestone, granite or whatever is local to your market for coarse aggregates. Crusher run weighs approximately 2,500 lbs. per cubic yard. The depth of the crusher run base recommended in inches will vary depending on the project. What is Crusher Run used for?
Feeding Size (mm) Capacity (t/h) Motor Power (kw) Moving cone Diemeter (mm) ... 245-730. 630. 1800. Features & Benefits. Limestone crusher features and benefits: Effective Crushing: With a large crushing capacity, limestone crushers are made for the effective crushing of limestone and related minerals. ... Crushed limestone is produced by ...
13.3.1.1 Primary Crusher. Primary crushers are heavy-duty rugged machines used to crush ROM ore of (−) 1.5 m size. These large-sized ores are reduced at the primary crushing stage for an output product dimension of 10–20 cm. The common primary crushers are of jaw and gyratory types.
Solutions. Limestone Crushing Process. The limestone crushing process involves several stages, each with specific machinery and equipment. The typical limestone …
The RM V550GO! is an impactor designed for difficult applications, so that you can reduce your machine investments and increase your profits. Primary crusher, secondary crusher and screener in one machine. Jaw & Impact Crushers to Crush Limestone Regardless of your mining volume, RUBBLE MASTER has a crusher for you. RM 100GO!
a bin. A feeder is used as illustrated in Figure 11.19.2-1. The feeder or screens separate large boulders from finer rocks that do not require primary crushing, thus reducing the load to the primary crusher. Jaw, impactor, or gyratory crushers are usually used for …
There are 2 main types impact crushers - horizontal shaft impact (HSI) crushers and vertical shaft impact (VSI) crushers. Horizontal Shaft Impactor (HSI) The horizontal shaft impactors are the most common impactor type that can be used in recycling, primary and secondary crushing applications. This type impactor will take reasonable size pieces ...
Limestone can be made into limestone powder by treatment of limestone crusher and limestone grinding mill. Limestone powder can produce quicklime by calcination. Quicklime can be widely used for desulfurization in power plants, and after adding water treatment to get hydrated lime. By mixing hydrated lime, lime slurry and lime paste can …
Primary crushers are first in a typical size reduction operation. Primaries like our Mega-Slam™ horizontal shaft impactor are commonly used in the aggregates industry to handle large feed sizes. The Grand-Slam™ HSI is well suited as secondary crusher for aggregate production for a wide range of materials including limestone, frac sand, gravel, stone, …
Why Choose The Jaw Crusher (APJ-110V)+ Impact Crusher (APF-1620H) in The Limestone Crushing Process? Jaw Crusher (APJ-110V): Serving as the primary crushing equipment, the jaw crusher boasts a high crushing ratio, consistent finished product size, reliable equipment performance, and a low failure rate.To fulfill the primary …
The Centerfeed Hammermill is a secondary crusher designed to accept feed from a primary with controlled top size ranging from 3" to 5" (75mm to 125mm). Industrial Hammermills are not limited to limestone or gypsum — they are known worldwide for processing bauxite, nickel ore, phosphate ore, coal, pet coke, clay, shale, and of course, …
As the term 'primary' implies, these crushers are used in the first stage on any size reduction cycle. The primary crusher is the link between chemical comminution (blasting) and the beginning of the mechanical comminution circuit (crushing and milling). The primary crushers take blasted, run-of-mine, or run-of-quarry feed up to 1500 mm and ...
The Impact Crusher is used for primary, secondary, fine crushing mining and rocks (for example, the granite, marble, and limestone) materials with compressive strength less than 350 MPa. The impact crusher is widely used for sand and rock producing in the industry of roads, railways, reservoir, electricity power and building materials and so on.
The term "primary crusher," by definition, might embrace any type and size of crushing machine. The term implies that at least two stages of crushing are involved, but in many cases the machine which performs the function of initial crusher is the only crusher in the plant. The factors influencing the selection of a crusher for this service ...
Crushing is the process of reducing the size of materials so that they can be further processed, the crushing process usually include 3 stages: primary crushing, secondary crushing, and the tertiary crushing. ... Crushing is also very useful in the chemical industry for breaking down hard materials such as limestone or coal. ... The …
Jaw crushers. Jaw crushers are used for the primary reduction of very hard and abrasive admixtures for cement manufacture. The reciprocating motion of the crushing jaw of the double – toggle (or Black type) jaw crusher subjects the material to a …
See more on vykin
WEBThe primary crusher receives the materials directly from the mine or quarry, and its size reduction ratio ranges from 3:1 to 7:1. The primary crusher can be a jaw crusher, gyratory crusher, or impact …
Willpactor®. Willpactors® are primary impact crushers with high capacities and large feed openings to accommodate run-of-mine limestone and rock. Willpactors® can be used as a primary limestone crusher, …
Defining the intended purpose of your primary crusher. The first step in choosing a primary crusher takes place at a high level. It's necessary to identify the purpose the crusher will be used for. This purpose is a given …
The difference between the cumulative percentages at the 3.5″ and 1.5″ points on the curve gives us the amount, of such product to be expected from the output of the primary crusher This is 85 minus 43, or 42% of the primary crusher product. If our problem had covered a crushing condition calling for 80 instead of 85% passing the …
After primary crushing, the crushed limestone is further reduced in size by secondary crushers. Common secondary crushers include cone crushers, impact crushers, or gyratory crushers. Screening. The crushed limestone is screened to separate different sizes of particles. This step ensures that the final product meets the required specifications.
Impact Crushers. Impact crushers are widely used in the crushing of various minerals and rocks, and are particularly suitable for the crushing of limestone with a low to medium hardness. They are characterized by a large crushing ratio, high efficiency, and good grain shape.
McLanahan offers a wide selection of Impact Crushers for quarried limestone and semi-abrasive minerals. McLanahan draws from the 75 years of field experience with the Universal line of Impactors, which includes impact breakers and Andreas-style impactors. At present, we offer the New Holland-style primary impact breaker and the MaxCap X …
Figure 5.1 is a typical sketch of a large gyratory crusher used as a primary crusher to reduce the size of large pieces of rocks produced during blasting in mines. Variations in the design of the breaking head and the mantle have been adopted by different manufacturers. Such variations are adopted from studies on stress distributions of …
The primary can produce these sizes at a rate of 150 to 12 000 mtph depending on the feed characteristics of the ore, the crusher setting, crusher size and the connected power …
This is the second stage of crushing. Feed size, which is around 150 to 300 mm, of the rock or ore from the primary crushing process is reduced to between 50 and 80 mm. Tertiary Crushing. This is the third stage of crushing. The size, which is around 50–80 mm, of the ore or rock from the secondary crushing process is reduced to between 5 …
2. Gyratory crusher. A gyratory crusher is one of the most in-demand primary crushers for stone crushing plants. It can process rocks, metal ores, granite, and other solid minerals of medium to high hardness. Gyratory crushers may be huge and capital-intensive, but they excel in high-capacity operations.
The crushing process involves the use of crushers to break down rocks and stones into smaller sizes. The primary crusher is used to reduce the size of the initial rocks, while the secondary crusher further breaks down the smaller pieces into finer materials. Purpose and Benefits of Using Primary and Secondary Crushers.
حقوق النشر © 2024.Artom كل الحقوق محفوظة.خريطة الموقع