Optimization of Mixing Equipment and Process for the …
This process, also called hydrophobation, is necessary in order to reach compatibility between the hydrophilic silica and the polymer. During this chemical reaction a silane, …
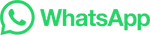
This process, also called hydrophobation, is necessary in order to reach compatibility between the hydrophilic silica and the polymer. During this chemical reaction a silane, …
In a typical CVC process, silica nanoparticles are produced by reacting silicon tetrachloride, SiCl 4 with hydrogen and oxygen . Difficulty in controlling the particle size, ... However, melt mixing process finds favor due to its compatibility with current industrial compounding facilities. In addition, the absence of solvents makes the process ...
3. 140 Add C the rest of the 5. Sequentially silica, and mix enter to 110 the °C interconnection. 4. 130 Sweep C and add oil, zone then and mix the to core 140 reaction °C and drop mixing zone. 5. 40 Sequentially rpm enter the interconnection zone and the core reaction mixing zone Twin rotor speed 40 rpm.
ABSTRACT: A wet mixing process is proposed for ・〕led rubber composites with a high silica loading to overcome the drawbacks of high energy consumption and workplace …
19.1 Introduction. Mixing processes are general operations in industrial process engineering. The main goal of these processes is to make a heterogeneous physical system homogeneous by using manipulating operations. Generally, efficient mixing can be challenging to achieve, especially on an industrial scale.
Furthermore, the mixing process necessitates a range of precision tools. Mixing blades are designed to ensure efficient dispersion and uniform distribution of additives and fillers throughout the silicone rubber matrix. These blades come in various shapes and configurations, each tailored to specific mixing methods. ...
A modified preparation of silica nanoparticles via sol–gel process was described. The ability to control the particle size and distribution was found highly dependent on mixing modes of the ...
well as an improved cooling system of all involved mixer components have become vital elements of an up to date mixer for silica compounds 7]. Nevertheless, also on the side of the[ mixing equipment, further improvements can be envisaged in order to realize an optimized mixing system for the production of silica compounds.
Bioinspired silica (BIS) has received unmatched attention in recent times owing to its green synthesis, which offers a scalable, sustainable, and economical method to produce high-value silica for a wide range of …
Process; Initial Mixing: Temperature Controller: 55 °C: 1. Add rubber, and mix for 15 s 2. Add carbon black, 1/2 silica, and the rest additives, then mix for 15 s 3. Add the rest of the silica, and mix to 110 °C 4. Sweep and add oil, then mix to 140 °C and drop 5. Sequentially enter the interconnection zone and the core reaction mixing zone ...
The sol-gel process is an inorganic polymerization considered a promising route for the design of new materials for optical, electrical, (bio)-medical and solar energy applications. Special ...
In order to efficiently prepare high-performance silica/rubber composites for use in the tread of semi-steel radial tires, a serial modular continuous mixer was designed according to the principle …
PDF | A wet mixing process is proposed for filled rubber composites with a high silica loading to overcome the drawbacks of high energy consumption and... | Find, read and cite all the...
PDF | On Dec 1, 2021, Zheng Ji and others published Mixing of cognate magmas as a process for producing high-silica granites: Insights from Guanmenshan Complex in Liaodong Peninsula, China | Find ...
The two types of wet mixing processes for silica-filled rubber composites are the in situ sol–gel method and the dispersion method. Utrera-Barrios et al. studied the effects of mixing methods (conventional and in situ sol–gel methods) for preparing …
As the earliest method, it is convenient and effective for the batch process to prepare silica nanoparticle . Nonetheless, the distribution of the particle size is wide and disorder due to the inhomogeneous mixing, especially for the large-scale synthesis . In this paper, we introduced microchannel as the mixer to adjust the hydrolysis ...
Mixing Considerations. Silicones sealants are rarely pure silicone. Additives are incorporated to reduce cost; improve mechanical, thermal, and electrical properties; and provide other characteristics such as pigmentation, improved bonding to substrates, and UV resistance. Silicones are typically filled with 15-30% by weight silica.
The formation reaction for the M–S–H gel is the main reaction in the MgO–SiO 2 –H 2 O system when the dosage of MgO is lower than 50%, while the formation reaction of Mg (OH) 2 is the main reaction when the dosage of MgO is higher than 50%. Based on the thermodynamic calculations, M–S–H gels are more stable than Mg (OH) 2.
The effects of the mixing time in a dry mixer were the main focus of that study. 18 The addition of a second filler was applied in the wet mixing process by Wang et al. who studied a 50 phr silica-filled natural rubber, using nanosilica modified with reduced graphene oxide. The silica-graphene fillers were directly mixed with the latex.
to be mixed into the rubber under optimized mixing conditions [2,3] using a suitable formulation [4] ... between the bound silane moieties and elastomer molecules during the curing process, chemical linkages between the silica and the elastomer molecules are created forming the basis for low rolling resistance tire treads. This filler ...
Under the OSHA Respirable Crystalline Silica Rule, employers are responsible for a range of measures to ensure that workers are protected from silica.. Measures include controlling dust levels below the …
Ascertaining how high-silica granites form is important for understanding why Earth has a high-silica continental crust and how the composition of the continental crust has evolved through time. This study presents a systematic dataset for the petrology, mineralogy, geochronology, and geochemistry of the granite porphyries and related …
contents of silica (60 phr) was prepared by a wet compounding and latex mixing process using a novel interface modifier cystamine dihydrochloride (CDHC) with coagulation ability . CDHC with the
Compared with the composites prepared by the conventional mechanical mixing method, the dispersion of both rGO and SiO 2 in the composites made by a wet compounding and latex mixing process is improved. As a result, the obtained silica/graphene/natural rubber composite prepared by this new method has good comprehensive properties.
The reduced graphene oxide (rGO) modified natural rubber composite (NR) filled with high contents of silica was prepared by a wet compounding and latex mixing process using a novel interface modifier …
The silica powder is dispersed prior to mixing with the latex during the wet mixing process, resulting in a more uniform dispersion of the silica filler, with comparatively low energy consumption ...
TLDR. In this study, triacetylcellulose (TAC) polymer-silica nanocomposite films are fabricated by deliberately designing a surface ligand that has a structure similar to that of polymer repeating units and effectively modifying the surface of silica nanoparticles through chemical bonding. Expand. 40.
Crystalline silica is a common mineral found in the earth's crust. Materials like sand, stone, concrete, and mortar contain crystalline silica. It is also used to make products such as glass, pottery, ceramics, bricks, and artificial stone. Respirable crystalline silica – very small particles at least 100 times smaller than ordinary sand you ...
A wet mixing process is proposed for filled rubber composites with a high silica loading to overcome the drawbacks of high energy consumption and workplace contamination of the conventional dry ...
In the tire industry, the combination of carbon black and silica is commonly utilized to improve the comprehensive performance of natural rubber so as to realize the best performance and cost-effectiveness. The corresponding mixing is divided into three processes (initial mixing, delivery, reactive mixing) by the serial modular continuous …
حقوق النشر © 2024.Artom كل الحقوق محفوظة.خريطة الموقع