Bauxite Mining and Alumina Refining
Bauxite mining and alumina refining are the upstream operations of primary aluminum production. This review article describes the industrial processes of …
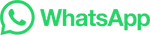
Bauxite mining and alumina refining are the upstream operations of primary aluminum production. This review article describes the industrial processes of …
For the latest statistics on bauxite/alumina production check the US Geological Surveys site. Production Figures Total bauxite production figures released by the Jamaica Bauxite Institute are measured as crude bauxite plus bauxite converted into alumina and in 1997 reached 3 million tonnes for the first quarter. This compared with a …
Bauxite is used to produce alumina, which is then used to produce aluminum. Wastes can be generated at several points in the production process, including during the mining of the bauxite ore, and during the refinery production process. The refinery processes used to produce aluminum generates about 2 – 2.5 tons of solid waste for …
The process for mining bauxite is not complex. Unlike ores from base metals, the grade of most bauxite found through mining is acceptable. Bauxites of Brazil, South-East Asia, as well as some types found in Australia and China, need up-grading from the crude ore. This is achieved by washing and screening, and then the super-fine …
There is a long process to transform bauxite, a critical raw material, into a substance with the required properties of cast aluminum alloys for use in electro automotive parts. Thanks to its unique properties, aluminum has become the material of choice for clean technology manufacturers in applications such as use in the automotive industry, …
About 80–85% of bauxite mined are processed to produce alumina and aluminium metal. Remaining 10–15% of crude bauxite is used in the non-metallurgical …
Magnetising roasting of the bauxite sample was conducted with 20-40% sawdust at temperatures between 870 o C and 880 o C. After magnetic separation, the major phase in the magnetic fraction was ...
The Bayer process is the principal method for the production of alumina from bauxite worldwide. The modern version of the process (developed in the 1880's) still maintains the key steps of dissolution of alumina-rich minerals into hot caustic solution, separation of the insoluble phases, followed by gibbsite precipitation and calcination of …
With the fast depleting of conventional crude oil reserves over the world, exploration, development and utilization of unconventional oils such as tar sands, ... XRD, FTIR and thermal analysis of bauxite ore-processing waste (red mud) exchanged with heavy metals. Clay Clay Miner., 56 (2008), pp. 461-469. View in Scopus Google Scholar
In this study, a crude untreated bio-diesel plant waste stream consisting of glycerol, methanol, free fatty acid salts and water was co-processed with Red Mud, the highly alkaline by-product of bauxite refining through the Bayer Process, at elevated temperature and pressure (350 to 400 °C; 0–500 psi hydrogen gas) in an attempt to ...
3. Iron-rich bauxite processing and metallurgy. Iron-rich bauxite ore usually contains over 40 wt% iron oxide [11, 12], huge reserves are found in Australia, Guinea, Brazil, Laos, Vietnam and China, but they have not yet been used effectively.It is worth noting that more than 1.5 billion tons of iron-rich bauxite resources have been explored …
Slurry-phase hydrocracking (SPHC) of unconventional heavy feedstocks is considered as a promising process to fill the gap between the ever-increasing demand …
Bauxite is generally extracted by open cast mining, being almost always found near the surface, with processes that vary slightly depending on the location. Before mining can commence the land needs to be cleared of timber and vegetation. Alongside this process may be the collection of seeds and/or saplings, for inclusion in a seedbank, which ...
12.1.2.1 Bayer Process Description - In the Bayer process, crude bauxite ore is dried, ground in ball mills, and mixed with a preheated spent leaching solution of sodium hydroxide (NaOH). Lime (CaO) is added to control phosphorus content and to improve the solubility of alumina. The resulting slurry is combined with sodium hydroxide and
Bauxite residue (red mud) is a solid waste produced in the process of alumina extraction from bauxite. More than 70 million tons of bauxite residue is generated annually. Presently, it is stored on land or in the ocean near alumina refineries. However, its high alkalinity is a potential pollution to water, land and air of close proximity.
3.1 Introduction to Crushing and Grinding of Bauxite. The most common initial process step to feed an alumina refinery with bauxite is the crushing or sizing of the raw bauxite material that is extracted from the mine. The feed material is crushed or sized so that it is conveyable, as well as correctly dimensioned, for the next step in the process.
42 the authors present the processing and the properties of a Brazilian refractory grade bauxite as a feasible substitute raw material for high-alumina refractories manufacturing,
Crude oil and natural gas are complex chemical mixtures that are generally unsuitable for direct use. Oil refining and gas processing turn these mixtures into a wide range of fuels and other products while removing low-value and polluting components. Refining and processing have both positive and negative environmental impacts: although they ...
To process the bauxite, the bauxite must be mined, crushed, and delivered to the refinery. The first step to reaching the refinery after mining the bauxite is crushing. The crushing …
Prices of bauxite in Ghana 2018-2023; Prices of crude oil in Ghana 2018-2023; ... Premium Statistic Forecast cumulative global mineral extraction and processing emissions 2050, ...
Bauxite deposit: geometrically defined space, geological unit composed of the bauxite body and its associated formations.In practice they are the subjects of the mining operation. Duricrust—cuirassé: Iron rich (Fe 2 O 3 % attains as much as 60–80%) layer developed on the topmost level of the laterite section in 0.2–0.3 m thickness It is …
The first process is known as distillation. In this process, crude oil is heated and fed into a distillation column. A schematic of the distillation column is shown in Figure 2.2 F i g u r e 2.2. As the temperature of the crude oil in the distillation column rises, the crude oil separates itself into different components, called "fractions.".
Bayer-process refineries with a combined alumina production capacity of 1.7 million tons per year produced an estimated 1.3 million tons in 2020, 8% less than that in 2019. ... free alongside ship (f.a.s.) for U.S. imports for consumption of crude-dry bauxite and …
Results of Washed Bauxite Processing by RDS Scrubbing process using RDS was aimed to increase alumina content by removing the impurities attached on the surface …
Abstract. Bauxite is processed in alumina refineries by the Bayer process in which Al-containing minerals are dissolved in hot NaOH. The insoluble solids (bauxite processing residue mud and sand) are washed, sometimes partially neutralized (using CO 2 or seawater treatment), and deposited in impoundments surrounding the refinery using …
Reactivity of various oxides present in bauxite vary with process conditions, hence, one way of enriching bauxite with Al 2 O 3 is by sequential separation of Fe 2 O 3 and TiO 2 and then further second stage chlorination of enriched bauxite. Alpha alumina form is not preferred for carbochlorination as it is a stable form [].Hence, the process …
In addition, draglines, front-end loaders, and power shovels are commonly used to excavate and load the crude ore. Loading is usually into haul trucks, or directly into rail cars or onto conveyor systems, for transport to bauxite processing facilities or stockpiles. Underground Bauxite Mining: IMAR 7th Edition
Ghana Bauxite Company Limited. First discovered in 1914 in Ghana by Sir Albert Kitson, bauxite is an ore and the main source of aluminium. Though the British Aluminium Company gave approval for …
Bauxite is the principle ore for the production of alumina and aluminum metal. Via a two-stage process that involves the refining of bauxite to alumina by the Bayer process, wet chemical caustic leach …
The mineralogy of the bauxites has a significant impact on the operation of the Bayer process for alumina production. Typically, the Bayer process produces smelter-grade alumina of 99.5% Al 2 O 3, starting from bauxite containing 30% to 60% Al 2 O 3. The main objective of the Bayer process is to extract the maximum amount of aluminum from the ...
حقوق النشر © 2024.Artom كل الحقوق محفوظة.خريطة الموقع