Multi-Compartment Rod/Ball Mill Evaluation on …
In mineral processing operations, the grinding circuit is a key step in the process to achieve the particle size and liberation required for the subsequent stage of the …
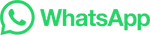
In mineral processing operations, the grinding circuit is a key step in the process to achieve the particle size and liberation required for the subsequent stage of the …
Ball Mill. A Ball Mill a type of grinder is a cylindrical device used in grinding (or mixing) materials like ores, chemicals, ceramic raw materials and paints. Ball Mills rotate around a horizontal axis, partially filled with the material to be ground plus the grinding medium. Different materials are used as media, including ceramic balls ...
This laboratory study investigates selective grinding and beneficiation options for a Greek bauxite ore. First, a series of batch grinding tests were carried out in order to investigate the ...
Bauxite milling machine, also known as grinding mill, is a crucial equipment in the bauxite ore beneficiation process. The purpose of this machine is to grind materials into powder form for further processing. The milling process involves three steps: crushing, grinding and classifying. Firstly, the bauxite ore is crushed into small particles ...
Bauxite ore is first mechanically pulverized and milled to reduce the particle size and then screened. The crushed ore is mixed with the process liquor containing caustic soda and processed in a grinding mill to produce a slurry containing 35–40% solids. Sodium hydroxide is the main chemical used in the process to extract aluminum hydrate ...
K is the grinding rate constant, t is the grinding time and M is a constant depending on the material properties and grinding conditions. The present laboratory study aims to investigate selective grinding and various beneficiation options for a Greek bauxite ore. First, selective grinding was carried out, through a series of batch
This laboratory study investigates selective grinding and beneficiation options for a Greek bauxite ore. First, a series of batch grinding tests were carried out in order to investigate the ...
Wet grinding of the bauxite ore in rod mills, ball mills, or semiautogenous grinding mills to produce fine slurry. Digestion of the slurry by caustic soda (NaOH) at strengths exceeding 170 g/L in vessels under pressure at temperatures ranging from 145 to 265°C depending on the type of bauxite being processed.
In one of our experiments for two stages beneficiation of Eastern Ghats bauxite, first the ore was screened by 1 mm sieve and coarser fraction was further treated in wet high intensity magnetic separation after grinding bauxite to −200 mesh (74 micron) size. First screening has substantially improved the grade as kaolinite and goethite ...
The present study through batch laboratory experiments aims to model grinding of bauxite ore and identify the optimum material filling volume in a ball mill. Modeling involves (i) the determination of the most suitable model, i.e., Gates–Gaudin– Schuhmann (GGS), Rosin–Rammler (RR), and logistic distributions, for describing
Bauxite recoveries in modern washing plants is in the range of 60–80%, however, in some of the plants, the recovery is found to be as low as 50%, as they use simple vibrating screens in place of hydro-cyclones. The quality of input bauxite, particularly silica content and targeted washed bauxite quality, dictate the washed ore recovery.
The grinding behavior of the bauxite ore was evaluated by identifying the relationship between the remaining mass (%) fraction of each particle size vs. grinding time. Figure 5a shows, as an example, the experimental data obtained for four selected sizes, namely 0.600, 0.300, 0.150 and 0.075 mm when the material filling volume (f c) …
bauxite grinding mill is mainly used to process mineral ores like bauxite, fineness from 80 mesh to 400 mesh, the whole equipment with low capital investment, and uses environmental protection ...
Bauxite is the major alumina (Al2O3) bearing ore used in the aluminum manufacturing industries. The bauxite containing less than 50% Al2O3 is called low-grade bauxite ore which is commonly used for the alumina-based abrasives and refractories productions. The alu-mina-silica and alumina-ferrite complexes are the fore-most impurities present in ...
HPGR grinding has been tested on laboratory and pilot scale for a number of bauxite ore s. These These bauxites did show to be relatively soft, in that th e compression resistance wa s low ...
PDF | This laboratory study investigates selective grinding and beneficiation options for a Greek bauxite ore. First, a series of batch grinding tests... | Find, read and …
Multi-objective multi-model predictive control for the continuous bauxite grinding process has been presented by Ma et al. (2012). The comparative analysis of three control strategies: single ...
In addition, grinding kinetic models were applied to the experimental data in order to identify if the linear theory of the population balance model is valid during bauxite grinding. The experimental data revealed that the logistic distribution is a model that represents more reliably particle size distributions obtained after grinding and fits ...
a) The ore of aluminium, bauxite, is concentrated by this method. The bauxite ore is contaminated with impurities of silica (SiO 2 ), iron oxides (Fe 2 O 3 ), titanium oxide (TiO 2 ), etc. b) Concentration is …
In the Bayer process, the particle size of the bauxite ore is first reduced through grinding, then it is sent to slurry transfer tanks, which are typically maintained at about 70°C. Pre-desilication is usually carried out in a series of continuously stirred tank reactors in which the temperature is maintained at 90°C to 100°C with high ...
Abstract. The most common process step to feed an alumina refinery with bauxite is sizing of the raw bauxite material that is extracted from the mine. The first …
Contact Now +86-. Published time:29 December 2022. Bauxite is an aluminum-containing mineral, and its main components include aluminum hydroxide, boehmite, diaspore, goethite, hematite, quartz, etc. Bauxite is formed from the parent rock in hot and humid climates. Its color is grayish-white, brown-red, and …
To process the bauxite, the bauxite must be mined, crushed, and delivered to the refinery. The first step to reaching the refinery after mining the bauxite is crushing. …
First Online: 23 January 2022. 708 Accesses. Part of the book series: Springer Series in Materials Science ( (SSMATERIALS,volume 320)) Abstract. The most common process step to feed an alumina refinery with bauxite is sizing of the raw bauxite material that is …
3 Physical Bauxite Processing: Crushing and Grinding of Bauxite 135. and Boehmitic bauxites are typically 1–3, while it ranges from 6½–7 for Diasporic bauxites [3]. Needless to say, the parameters corresponding to the bauxite being considered as feed to a new alumina refinery needs to be determined by laboratory testing based on samples ...
Open. Metrics. Abstract. Objective: To describe bauxite mining and alumina refining processes and to outline the relevant physical, chemical, biological, ergonomic, and …
Metallurgical bauxite is a low-value bulk ore, and therefore preference is often given to simple beneficiation techniques, such as crushing followed by dry screening or washing and scrubbing ...
Bauxite is the major alumina (Al 2 O 3) bearing ore used in the aluminum manufacturing industries.The bauxite containing less than 50% Al 2 O 3 is called low-grade bauxite ore which is commonly used for the alumina -based abrasives and refractories productions. The alumina -silica and alumina -ferrite complexes are the …
This Table of Ball Mill Bond Work Index of Minerals is a summary as tested on 'around the world sample'. You can find the SG of each mineral samples on the other table. Source 1. Source 2. Source 3. Source 3. Source 4.
This laboratory study investigates selective grinding and beneficiation options for a Greek bauxite ore. First, a series of batch grinding tests were carried out in order to investigate the grinding behavior of the ore and the effect of the material filling volume (fc) on the distribution of aluminium- and iron-containing phases.
حقوق النشر © 2024.Artom كل الحقوق محفوظة.خريطة الموقع