Key Factors for Ball Mill Optimization in the Mining Industry
Successful ball mill optimization in the mining industry requires careful consideration of a range of factors, including mill design, operating conditions, grinding media properties, feed material properties, particle size distribution, and slurry rheology. Addressing these factors can lead to significant improvements in grinding efficiency ...
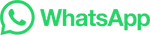