Special issue on ultrafine particles: where are they from and …
Particles are usually defined based on their size: coarse particles are those with a diameter of 10 μm or less (PM10), fine particles are those with a diameter of 2.5 μm or less (PM2.5), and ...
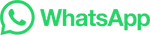