Review on vertical roller mill in cement industry & its …
2.3. Raw meal drying, grinding, and homogenization. Raw mix, high grade limestone, sand and iron ore are transported from their bins to raw mills for drying and further fine grinding. The raw mill is either a Ball mill with two chambers or Vertical roller mill with inbuilt classifier.
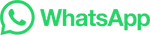