IELTS Writing Task 1 – Cement and concrete making process
It is clear that there are five stages in the production of cement, beginning with the input of raw materials and ending with bags of the finished product. To produce concrete, four different materials are mixed together. At the first stage in the production of cement, limestone and clay are crushed to form a powder.
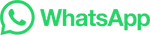