(PDF) A Review of Advanced Ball Mill Modelling
Symbols are experimental data and lines model predictions (0.3 m mill, 40 mm steel balls, 30 % filling, 100 % interstitial filling, 67 % of critical speed). Figures - uploaded by Luis Marcelo Tavares
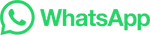
Symbols are experimental data and lines model predictions (0.3 m mill, 40 mm steel balls, 30 % filling, 100 % interstitial filling, 67 % of critical speed). Figures - uploaded by Luis Marcelo Tavares
How to design a Ball Mill (4 replies) E= 10 Wi (1/√P80- 1/√F80) E= Specific Energy, Wi= Work Index,P80= Output,F80= Feed. After this we need to multiply certain factors such …
Chemical process industries are running under severe constraints, and it is essential to maintain the end-product quality under disturbances. Maintaining the product quality in the cement grinding process in the …
Blagoy Sokolov. Stefan Stoenchev. Citations (54) References (78) Figures (6) Abstract and Figures. The paper presents an overview of the current methodology and practice in modeling and …
22 May, 2019. The ball mill consists of a metal cylinder and a ball. The working principle is that when the cylinder is rotated, the grinding body (ball) and the object to be polished (material) installed in the cylinder are rotated by the cylinder under the action of friction and centrifugal force. At a certain height, it will automatically ...
Ball mills, conversely, contain grinding media up to 50mm in diameter, occupying between 25% - 40% of mill chamber volume. To effectively reduce material size, each type of mill needs to generate different charge load actions, or the type of motion characterised by the mill's contents. SAG mills generate higher levels of impact reduction and ...
A ball mill consists of various components that work together to facilitate grinding operations. The key parts include the following: Mill Shell: The cylindrical shell provides a protective and structural enclosure for the mill. It is often made of steel and lined with wear-resistant materials to prolong its lifespan.
1. Fill the container with small metal balls. Most people prefer to use steel balls, but lead balls and even marbles can be used for your grinding. Use balls with a diameter between ½" (13 mm) and ¾" (19 mm) inside the mill. The number of balls is going to be dependent on the exact size of your drum.
1.Axial/radial runout. 2.Alignment of the drive trains. 3.Uneven power splitting. 4.Centre distances variable. 5.Face load distribution. 6.Sealing of the girth gear. 7.Girth gear is through hardened only, fatigue strength is limited. -Dynamic behaviour. -A lot of individual rotating masses risk of resonance vicinities.
Grinding Mill Gear Assembly. We will begin with the mill's bull gear assembly and work towards the motor, The BULL GEAR, sometimes called the RING GEAR is designed to turn the mill transforming the energy of the motor into motion for the mill. By mill we refer to Ball Mills, Rod Mills and SAG Mills. Anything gear and pinion …
26600 Pekan, Pahang, Malaysia, Phone: +6094246255; Fax: +6094246222. *. Email: [email protected]. ABSTRACT. This project is to design and fabricate the mini ball mill that can grind the solid ...
A ball mill also known as pebble mill or tumbling mill is a milling machine that consists of a hallow cylinder containing balls; mounted on a metallic frame such that it can be rotated along its longitudinal axis. …
spacing and height of lifter bars, and to minimize liner/lifter and ball damage by avoiding. impact onto the mill shell. This paper presents a short review of mill liner design and its effects on ...
Small Ball Mill Capacity & Sizing Table Ball Mill Design/Power Calculation
still require development until the technology becomes ready for being used for optimizing and designing ball mills. Finally, the advances recently accomplished on the approach …
According to the specifications and parameters of the ball mill, the general layout, grinding body, lining plate, partition device, support device, transmission part and …
If a ball mill uses little or no water during grinding, it is a 'dry' mill. If a ball mill uses water during grinding, it is a 'wet' mill. A typical ball mill will have a drum length that is 1 or 1.5 times the drum diameter. Ball mills with a drum length to diameter ratio greater than 1.5 are referred to as tube mills.
Planetary ball mills with higher energy input and a speed ratio of 1:-2.5 or even 1:-3 are mainly used for mechanochemical applications. Click to view video. Planetary ball mills - Fields of application. Planetary ball mills are used for the pulverization of soft, hard, brittle, and fibrous materials in dry and wet mode. Extremely high ...
The one of main problem in cement industry is the continouse abrasion in lining plates of cement mill as a result of impact, abrasive and erosion by steel balls grinding media inside cement mill.
Ball Mill Design Parameters. Size rated as diameter x length. Feed System. One hopper feed; Diameter 40 – 100 cm at 30 ° to 60 ° Top of feed hopper at least 1.5 meter above the center line of the mill.
Running a pilot ball mill circuit can overcome this problem but this requires a reasonably large sample and therefore can be costly. In addition a valid scale-up procedure is required. To overcome these limitations in using modelling and simulation for designing ball mill circuits, a programme of research was initiated at the JKMRC in …
Ball mills and grinding tools Cement ball mills are typically two-chamber mills (Figure 2), where the first chamber has larger media with lifting liners installed, providing the coarse grinding stage, whereas, in the second chamber, medium and fine grinding is carried out with smaller media and classifying liners.
Materials Science and Engineering, A168 (1993) 149-152 149 Designing a high energy ball-mill for synthesis of nanophase materials in large quantities D. Basset, P. Matteazzi* and F. Miani Dipartimento di Scienze e Tecnologie Chimiche, Universitd degli Studi di Udine, Via Cotonificio 108, 1-33100 Udine (Italy) Abstract …
Ball Mill Grinding Process Handbook - Free download as PDF File (.pdf), Text File (.txt) or read online for free. This document provides guidance on ball mill grinding processes. It covers topics such as ball mill design including length to diameter ratios, percent loading, critical speed, and internals evaluation. Methods for assessing ball charge, wear rates, …
A pharmaceutical ball mill is a type of grinder used to grind and blend materials while manufacturing various dosage forms. The size reduction is done by impact as the balls drop from near the top of the shell. Ball mills are used primarily for single-stage fine grinding, regrinding, and as the second stage in two-stage grinding circuits.
partition device, support device, transmission part and feeding and discharging device of the ball. mill are designed. In this paper, the design method of three chamber ball mill is introduced ...
The ball mill contains a hollow cylindrical shell that rotates about its axis. This cylinder is filled with balls that are made of stainless steel or rubber to the material contained in it. …
i am designing rubber lining for ball mill with below given operating condition can you please suggest me approximate thickness of shell liners and lifter bar ? OPERATING CONDITIONS: 1. MATERIAL : MAGNETITE ORE + URANIUM ORE (COMBINED) 2. FEED SIZE : MAGNETITE ORE, 80% (-) 125microns & URANIUM ORE, 80% (-) 75MICRONS
Afquip Africa offer Mill Liners for SAG, AG, Rod and Ball Mills in a range of material specifications according to client requests, Mill type and Liner Profiles which include Manganese, Manganese Chrome, High Chrome, Ni-Hard 4 and or other specific requirements. Afquip Africa is capable of offering Mill Liner designs services which …
In extract from Process Machinery Reference Manual I willingly also provide 2 Ball Mill Sizing (Design) example done 'by-hand' out tables additionally charts. Today, much of this mill designing is done by computers, power models and others. These are a good back-to-basics vigorous for those wanting until understand …
حقوق النشر © 2024.Artom كل الحقوق محفوظة.خريطة الموقع