Crusher Product Gradation Charts
Crusher manufacturers publish grid charts, particle size cumulative distribution curves, and/or product size distribution tables to help predict the gradation of the crusher product. These charts, curves, and tables give the percentages passing or retained on standard size screens for each given setting of the crusher.
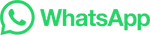