Meeting the needs of an exacting market
salts, beneficiation is achieved by grinding to a maximum grain size of 0.8-1.0 mm. For the coarser sylvinite ores as found in Saskatchewan, a size reduction to <9 mm would give an adequate liberation. POTASH ORE PROCESSING Meeting the needs of an exacting market The production of marketable potash from the basic ore may comprise a
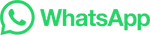