Powder metallurgy – basics & applications
Vibratory ball mill • Finer powder particles need longer periods for grinding • In this case, vibratory ball mill is better => here high amount of energy is imparted to the particles and milling is accelerated by vibrating the container • This mill contains an electric motor connected to the shaft of the drum by an elastic coupling.
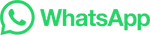