HP series cone crushers Wear parts …
passing point. A typical reduction ratio in the HP standard cavity is 3-5 and in the HP short head cavity it is 2-4. Wear parts application guide - HP series cone crusher HP cone crusher and basic concepts Product Feed Reduction ratio = F80 / P80
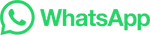