Cone crusher basics in 4 minutes
Inside your cone crusher The basic principle is straightforward: the material to be crushed (the feed), drops into the crushing chamber. The mantle is a moving part that gyrates in …
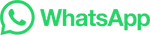
Inside your cone crusher The basic principle is straightforward: the material to be crushed (the feed), drops into the crushing chamber. The mantle is a moving part that gyrates in …
Cone crusher with large stroke for maximum crushing capacity; 3-arm crusher design for high throughput; ... When the desired function is selected, clear instructions guide users through all operating steps. If a fault occurs, a fault diagnosis appears on the display. Fault localization, the description and remedy tips result in reduced downtimes.
A cone crusher is a super important machine used in mining and construction. It's designed to break down big rocks, ores, and other stuff into smaller pieces that are easier to handle. ... Function; Crushing Chamber: Central part of the crusher: Houses the crushing process: Consists of the bowl liner (fixed outer cone) and mantle …
Cone crusher basics in 4 minutes This is the starting point for understanding how cone crushers work – and how they can make your mine or quarry more productive. ... for essential site functions, analyzing site performance, personalizing content, and delivering targeted ads. Some cookies are necessary and can't be turned off, while others ...
Mellott has the expertise to properly size and select the optimal cone crushers for your purposes. Contact us today at 888.621.8533 or online to discuss how we can maximize your cone-crushing productivity. This entry was posted in …
The Cone crusher mantle is one of the main components of the cone crusher, also known as the moving cone. The mantle is forged with new composite materials, which have the characteristics of super …
The cone crusher (Fig. 13.12) is very similar to the gyratory type, except that it has a much shorter spindle with a larger-diameter crushing surface relative to its vertical dimension. The spindle is not suspended as in the gyratory crusher. ... Schematic diagram depicting the basic elements and function of a cone crusher. A working cone ...
Cone crusher and gyratory crusher work on the same principle. Both have the same operation. If cone crusher differs then it is only from crushing chamber. Cone crusher has a less steep crushing chamber and more parallel zone between crushing zones. It breaks the rocks by squeezing it between the gyrating spindles.
The capacity is a function of size and OSS. Manufacturers publish tables of capacity for their crushers of various size as a function of the open-side set. 5.1.1 Cone crushers Cone crushers are commonly used for secondary, tertiary and quaternary crushing duties. Two variations are available - standard and short head
This paper reports the calibration and validation of a cone crusher model using industrial data. Usually, there are three calibration parameters in the condensed breakage function; by contrast, in this work, every entry of the lower triangular breakage function matrix is considered a calibration parameter. The calibration problem is cast as …
A cone crusher is a super important machine used in mining and construction. It's designed to break down big rocks, ores, and other stuff into smaller …
A cone crusher is one of many different types of crushers, like impact crushers, jaw crushers, and hammermills, that is used to process and reduce material like aggregates and construction and demolition waste. The cone crusher distinguishes itself from these other crushers by how it operates in processing material. Similar to the jaw …
Cone Crusher. Cone crusher is a type of crushing equipment whose crushing cone rotates in the conical cavity within the shell to realize intermediate crushing or fine crushing of material through squeezing, bending, shearing, and impacting. At the end of the nineteenth century, the Simons brothers of the USA invented this equipment …
® MP Series™ cone crushers are known for having the highest crushing force of any cone crushers similar in size. Suitable for reducing and shaping both hard rock and soft rock, these crushers are designed especially for mining applications. High availability. Automation and maintained crusher force with a hydraulic clearing system.
Cone crusher wear parts include mantles, concaves, ... Understanding the different types of wear parts and their functions, as well as the factors to consider when selecting the right wear parts, is crucial for optimizing equipment performance and reducing maintenance costs. Investing in high-quality wear parts provides many benefits, including ...
19. HP Series cone crushers 3. Proven and predictable production. HP Series cone crushers provide predictable and consistent capacity, end product size, gradation and shape, making them a safe choice for aggregates and mining processes. The crusher setting is mechanically fixed while crushing and it is secured by dual-acting cylinders ...
38-64. 380. 344-798. 550-1098. 710-1398. 800-1498. We increase the value of the High quality cone crusher manual function production by improving the technology, which enables us to achieve greater profits. Adhering to the tenet of 'quality first, reputation first, service first', we have won the recognition and praise of our customers.
A cone crusher punishes itself in every minute of operation. It squeezes a dense mass between heavy castings until the mass disintegrates. It abrades and minces aggregate until the material yields …
cone crushers are an excellent choice in secondary, tertiary, quaternary and pebble-crushing applications. They are equipped with the hydraulic Hydroset™ system, which provides safety and setting …
In summary, a cone crusher operates by rotating the mantle and the concave at high speeds, which compresses and breaks down rocks into smaller pieces. The gap between the mantle and the …
Cone crushers are versatile machines, but using them as they are set up to function is the best idea. A 4:1 reduction ratio is a standard crusher application. Opting to use it for a 6:1 or 8:1 reduction of material could fall outside the parameters of its intended function, with punitive impact on the machine.
Similar to jaw crushers, cone crushers are another compression crusher that aggregate, concrete, mining, natural gas …
A common type of machine used as secondary and tertiary crushers, is the cone crusher. Previous research (Evertsson, 2000; Gauldie, 1953) has made it possible to model the behaviour of a given cone crusher. The geometry of the crushing chamber is crucial for the performance. ... Power draw, hydroset pressure and capacity as a …
See more on savree
WEBCone crushers are powerful machines that are commonly used for secondary and tertiary crushing in the mining and aggregate industries. These machines …
Each crusher is a complex unit with a large number of parameters. For example, a cone crusher is represented by a system with six degrees of freedom with two symmetry planes. The basic dependencies and formulas for the mathematical description of the cone crusher have been suggested .
Cone crushers are commonly used for secondary, tertiary and quaternary crushing duties. Two variations are available - standard and short head. The chief difference between …
The function of the primary crusher is to break down the larger rocks and stones into manageable sizes, while the function of the secondary crusher is to further refine these sizes into the desired …
The cone crusher is a modified gyratory crusher. The essential difference is that the shorter spindle of the cone crusher is not suspended, as in the gyratory, but is supported in a …
The size reduction process of rocks in cone crushers is one of the most important issues, particularly for the secondary and tertiary stages of crushing operations. In this study, 17 different rock types were considered for the evaluation of their size reduction variations that occurred in a laboratory-scale cone crusher. Based on several …
ring bounce. Depending on the crusher characteristics of the rock, this setting can change. 2. Feed opening "B" is at a minimum setting "A". 3. Maximum feed size vary from 80 to of "B" depending on the machine size and material. Each HP cone crusher has several cavity options with different feed openings and setting ranges.
حقوق النشر © 2024.Artom كل الحقوق محفوظة.خريطة الموقع