Iron Ore Facilities :: Cleveland-Cliffs Inc. (CLF)
Cleveland-Cliffs recently completed a $100 million expansion at its Northshore Mining operation to support large-scale commercial production of DR-grade pellets. With its completion, Northshore Mining is now the …
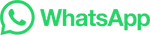