Friction and wear of liner and grinding ball in iron …
Friction and wear of liner and grinding ball in iron ore ball mill - ScienceDirect. Article preview. Abstract. Introduction. Section snippets. References (38) …
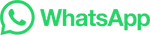
Friction and wear of liner and grinding ball in iron ore ball mill - ScienceDirect. Article preview. Abstract. Introduction. Section snippets. References (38) …
DOVE Ball Mills are highly efficient grinding mills designed to grind and blend bulk material ranging from soft, fibrous to hard and brittle material. DOVE Ball Mills are …
The most important disturbances to the process are ore hardness changes and feed . size variations. ... Ball mills can grind a wide range of materials, including metals, ceramics, and polymers ...
Ball mills tumble iron or steel balls with the ore. The balls are initially 5–10 cm diameter but gradually wear away as grinding of the ore proceeds. The feed to ball mills (dry basis) is typically 75 vol.-% ore and 25% steel. The ball mill is operated in closed circuit with a particle-size measurement device and size-control cyclones.
The present work demonstrates the application of the mechanistic UFRJ ball mill model to predict fine grinding of iron ore in a pelletizing plant in Brazil, the first application of such a ...
An Itabirite iron ore sample with a top particle size of 19 mm was tested in another batch ball mill with a diameter of 580 mm and a length of 240 mm. Analysis of the grinding operation presented an operating work index of 14.7 kWh/t. Grinding times varied from 1 to 16 min. Top ball size was set to 63 mm, mill filling of 27 % and 76 % of ...
1 Population balance model approach to ball mill optimization in iron ore grinding Patricia M. C. Faria1,2, Luís Marcelo Tavares2 and Raj K. Rajamani3 1. Vale S.A., Brazil 2. Department of ...
A ball mill is still the preferred solution for many types of dry grinding duty. A ball mill consists of a rotating horizontal cylinder, containing a cascading grinding media, typically steel or ceramic balls, in the range of 10 to 100 mm diameter. The grinding mechanism takes place within the falling and sliding grinding media.
The present investigation involves the identify the physical properties of three different types of iron ores by using Bond ball mill. The result shows that the maximum Bond work index of 14 KWh ...
The ball mill is a rotating cylindrical vessel with grinding media inside, which is responsible for breaking the ore particles. Grinding media play an important role in the comminution of mineral ores in these mills. This work reviews the application of balls in mineral processing as a function of the materials used to manufacture them and the …
Vertimill® has 50% less footprint than a ball mill. Lower operating cost Vertimill® is an energy efficient grinding machine. ... grinding mill at Miaogou Iron Mine to achieve the ... an increase in grinding fineness from 71-73% to 88-90% passing -325 mesh, increase from 65% to 66% in iron ore concentrate and an average recovery increase from ...
1 Introduction. Modern iron ore pelletizing process operations may be divid-ed into two main process sections: feedstock preparation and agglomeration processes. In most …
The particle breakage of the ball mill is an extremely complicated breakage process. It is difficult to quantify and describe the particle breakage behavior. In this study, a drop-ball experimental setup was developed to demonstrate the impact process of grinding media on ore particles.
Contact Us. Ball Mills. Ball mills have been the primary piece of machinery in traditional hard rock grinding circuits for 100+ years. They are proven workhorses, with discharge …
Grinding circuit data and ore samples were collected from nine industrial ball mills of diameters 3.2-5.5 m. For each of the ores tested there is a simple relation between the parameter and ...
Abstract: The ball mill is a rotating cylindrical vessel with grinding media inside, which is respon-sible for breaking the ore particles. Grinding media play an important role in the …
Ball mills have been the primary piece of machinery in traditional hard rock grinding circuits for 100+ years. They are proven workhorses, with discharge mesh sizes from ~40M to <200M. Use of a ball mill is the best …
At Carajas, the new grinding plant was operational in 2002, with two ball mill lines followed by a de-sliming plant. The closed circuit, wet grinding mills were designed to operate at 600% circulating load, in order to minimize the production of fine particles and consequently give increased recovery at the de-sliming plant.
Peng et al. 24 used the ball cratering method to design a test rig that mimics the contact friction and wear between charge and lifter in the grinding zone of the ball mill. Noaparasat et al. 25 ...
DOVE Ball Mills are designed to operate with various types of grinding media (Grinding Balls), DOVE supplies various types and sizes of Ball Mills Balls. DOVE supplies Steel Balls in Various sizes and …
The sample of coarse iron ore was characterized in laboratory tests carried out in a small batch ball mill. Selection and breakage function parameters were determined from the laboratory tests.
Steel-Head Ball-Rod Mills are available in any one of five different types of discharge: 1. Overflow, 2. perforated overflow, 3. return spiral, 4. grate, and 5. peripheral. To best serve your needs, the Trunnion can be furnished with small (standard), medium, or large diameter opening for each … See more
Crushed ore is fed to the ball mill through the inlet; a scoop (small screw conveyor) ensures the feed is constant. For both wet and dry ball mills, the ball mill is charged to approximately 33% with balls (range 30-45%). Pulp (crushed ore and water) fills another 15% of the drum's volume so that the total volume of the drum is 50% charged.
Ball mill is a common grinding equipment in concentrator, the main role is to provide qualified grinding products for the subsequent dressing process. ... • Peripheral ball mill: Discharge the ore through the periphery of the cylinder. ... 8 Types of Iron Ore Magnetic Separator. (04:03:13) Research on Vat Leaching Test of A Small ...
The ball mill is a rotating cylindrical vessel with grinding media inside, which is responsible for breaking the ore particles. Grinding media play an important …
These features distinguish stirred mills as fundamentally different from both ball mills and Tower Mills, as demonstrated by Tables 1 and 2. Table 1 : Typical Power Intensities of different Grinding Devices Table 1: Power Intensity of Different Grinding Devices Ball Mill is a 5.6m D x 6.4m L @ 2.6MW Tower Mill is a 2.5m D x 2.5m L @ 520KW
The grinding process for all the three iron ores is carried out individually in Bond's ball mill and the total retention time taken by each iron ore sample is calculated. The present investigation focuses on utilizing the calculated retention time of the iron ore as a standard grinding reference time to the laboratory ball mill for optimizing ...
How a Ball Mill Works. Ball mills work by using balls to grind materials. Materials such as iron ore, pain and ceramics are added to the ball mill. Next, the ball mill is activated so that it rotates — either …
An iron ore concentrate sample was ground separately in a pilot-scale HPGR mill in multiple passes and a dry open-circuit ball mill to increase the specific surface area of particles.
The paper demonstrates the application of this methodology to optimize solids concentration in ball milling of an iron ore from Brazil. The wet grinding experiments were conducted in bench (0.25 m diameter) and pilot-scale mills (0.42 m diameter), and surveys in a full-scale industrial (5.2 m diameter) mill.
حقوق النشر © 2024.Artom كل الحقوق محفوظة.خريطة الموقع