Steel Making Process – Complete Overview with Flowchart
In the open hearth process for producing steel, pig iron, steel scrap, and iron oxide in the form of iron ore or scale are melted in a Siemens-Martin open hearth furnace (Fig. 4.4), so called because the molten metal lies in a comparative shallow pool on the furnace bottom or hearth. The hearth is surrounded by a roof and walls of refractory ...
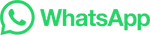