Advanced Analytics for Mineral Processing
Froth flotation is one of the most widely used and most efficient ore beneficiation methods to effectively process complex metallic ores and produce clean …
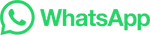
Froth flotation is one of the most widely used and most efficient ore beneficiation methods to effectively process complex metallic ores and produce clean …
Residual unreacted Cr(VI) incorporated in ferrous-sulfate-reduced chromite ore processing residue (rCOPR) can be slowly released during deposition, posing a significant threat to the environment.Recent studies …
Countries such as the as Czech Republic and Hungary, however, have already banned the use of cyanide in gold ore processing. ... bioxidation and ultra-grinding techniques are becoming increasingly more efficient, facilitating the processing of complex gold ores. In terms of alternative leaching reagents, several avenues have been explored …
2.4. Beneficiation methods. Beneficiation is a process where ore is reduced in size and valuable minerals are separated from the gangue minerals. Separation of valuable minerals from gangue minerals can be efficiently achieved by taking advantage of the differences in physical, surface, and magnetic properties.
Volume 160, September 2020, 104919. Review. Near-zero-waste processing of low-grade, complex primary ores and secondary raw materials in Europe: technology development trends. Author links open overlay panel. Jeroen Spooren a., Koen Binnemans b, …
Efficient immobilization and utilization of chromite ore processing residue via hydrothermally constructing spinel phase Fe2+ (Cr3+X, Fe3+2-x)O4 and its magnetic …
In summary, the following kinetic equation can be applied to describe the pressure leaching process for chromite ore in 50 wt% KOH solution: (3) 1 - ( 1 - x) 1 / 3 = 20537 × ( P O 2) 1.16 × e - 64020 RT × t. The reaction activity of KOH solution decreases significantly with the decrease of KOH concentration, while the oxygen solubility and ...
Overview of chromite ore processing. Chromite ore FeO·Cr 2 O 3 is a major ore for Chromium. India accounts for about 10% of world share of shipping grade Chromium ore reserves, having 45% Cr 2 O 3 content. South Africa and Zimbabwe and India are the Top five countries of Chrome ore processing industries in the Word (Indian Minerals …
For chrome ores, gravity separation is often used to process denser mineral particles. By using efficient equipment such as chutes, jigs, and shakers, the efficiency of gravity selection can be ...
Mekanism Ore Processing Guide Mekanism offers multiple tiers of ore processing, each providing a greater yield from your ores. This guide will walk you through each tier, the machines needed, and how to progress to the next tier. Tier 0: Basic Smelting This is the base Minecraft method of directly smelting ores into ingots.
Chromite ore processing residue (COPR), derived from the so-called high lime processing of chromite ore, contains high levels of Cr(III) and Cr(VI) and has a pH between 11 and 12. Ferrous sulfate, which is used for remediation of Cr(VI) contamination in wastewater and soils via reduction to Cr(III) and subsequent precipitation of …
Fig. 1 illustrates the mineralogical characteristics of siderite ore. It can be seen that the siderite was the dominate mineral in the raw ore. The calcium and magnesium existed in dolomite (CaMg(CO 3) 2) and ankerite (Ca(Mg,Fe) (CO 3) 2) particles with size of 100–300 microns.The distribution of potassium and aluminum were consisted with the …
THE DOMESTIC IRON ORE MINING AND STEEL INDUSTRIES BENEFITS • Greater efficiency at separating out problematic, weakly magnetic middlings particles, resulting in a cleaner, value-added iron ore product • Process energy savings of 4.2 GWhrs at 3.5 cents per kWh, saving approximately $150,000 per million tons of processed ore or
Within an ore body, valuable minerals are surrounded by gangue and it is the primary function of mineral processing, to liberate and concentrate those valuable minerals. 1.3 Run-Of-Mine Material and Minerals. Generally, mineral processing begins when an ore is delivered from a mine, to a processing facility.
Chromite ore processing residue (COPR) has been a severe environmental contaminant which is worthy of attention. In this study, we developed an eco-friendly and practical technology for effectively stabilizing and recovering Cr(VI) in COPR via combining FeSO 4 reducing agent and the hydrothermal treatment. A stable spinel phase product …
Residual unreacted Cr(VI) incorporated in ferrous-sulfate-reduced chromite ore processing residue (rCOPR) can be slowly released during deposition, posing a significant threat to the environment. Recent studies indicate that such Cr(VI) mainly exists within the nano-sized ion channels of ettringite, forming Cr(VI)–ettringite. Therefore, efficient extraction and …
Size reduction is a necessary operation in mineral processing plants and provides the desired size for separation operations and the liberation of the valuable minerals present in ores. Estimations on energy consumption indicate that milling consumes more than 50 % of the total energy used in mining operations. Despite the fact that ball …
Chromium ore processing residue (COPR) is a hazardous waste generated during the production of chromate. Currently, approximately 10% of Cr 2 O 3 cannot be extracted after chromite sodium roasting and remains in COPR, wasting valuable Cr resources. In this study, Mg was selectively removed by using (NH 4) 2 SO 4 roasting in …
8.2: Mining and Ore Processing. Page ID. Steven Earle. Vancover Island University via BCCampus. Metal deposits are mined in a variety of different ways …
mineral processing, art of treating crude ores and mineral products in order to separate the valuable minerals from the waste rock, or gangue. It is the first process that most ores undergo after mining in order to provide …
Fluorite ore beneficiation is a complex process involving various stages of extracting the fluorspar mineral from its original form. The process typically involves crushing, grinding and flotation methods to separate valuable fluorspar from other impurities. An interesting aspect of fluorspar ore beneficiation is the use of advanced …
In order to solve the problems of a slow solving speed and easily falling into the local optimization of an ore-blending process model (of polymetallic multiobjective open-pit mines), an efficient ore-blending scheduling optimization method based on multiagent deep reinforcement learning is proposed. Firstly, according to the actual …
The emerging flash ironmaking technology, which is highly efficient and has low pollutant emissions, has become an option. This article uses CFD software to …
This process is highly efficient and has been extensively used for beneficiating magnetite ores. ... The beneficiation of various types of iron ore is a complex process that requires careful analysis and planning. Whether it is hematite, magnetite, or any other iron ore, implementing effective beneficiation technology can significantly …
Efficient immobilization and utilization of chromite ore processing residue via hydrothermally constructing spinel phase Fe2+(Cr3+X, Fe3+2-x)O4 and its …
A study into the options for a 10 Mtpa ore processing plant for a hard, fine-grained, silica-rich magnetite ore was carried out, with the emphasis on comminution circuit options. ... It can be expected that highly energy-efficient autogenous processing routes would be further developed and increasingly applied in practice. Authors: Alex ...
Relatively deep deposits, or those with elongated or irregular shapes are typically mined from underground with deep vertical shafts, declines (sloped tunnels) and levels (horizontal tunnels) (Figures 8.2.1 and 8.2.2). In this way it is possible to focus the mining on the orebody itself. In some cases, the near-surface part of an orebody is ...
In India, where iron ore processing is one of the major industries, the generation of tailings is estimated to be 10-25 % of the total iron ore mined, amounting to 18 million tons per year (Das et al., 2000 ). The tailings contain silica in high percentage (40-60 %, from various locations). This makes it a suitable raw material for the ...
The mineral processing industry, a prominent element of modern industrial economies, is crucial for extracting valuable minerals from ores [].This fundamental …
Current mining and processing operations tend to have low recoveries, on the order of 50–80%, from ore to high-purity REE compounds. 5 Inefficient recovery is partly due to the low intrinsic value of the geologic resource compared with the processing costs. The processes for REE ores have been characterized by occasional major developments …
حقوق النشر © 2024.Artom كل الحقوق محفوظة.خريطة الموقع