Beneficiation Strategies for Removal of Silica and …
The technologies applicable to beneficiating iron ore fines include wet and dry gravity and magnetic separation, flotation, and roasting followed by magnetic …
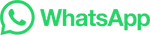
The technologies applicable to beneficiating iron ore fines include wet and dry gravity and magnetic separation, flotation, and roasting followed by magnetic …
Abstract. This chapter introduces the principle of how low-grade iron ores are upgraded to high-quality iron ore concentrates by magnetic separation. Magnetite is the most magnetic of all the naturally occurring minerals on earth, so low-intensity magnetic separators are used to upgrade magnetite ores. On the other hand, because oxidized …
Next. Beneficiation of Iron Ore and the treatment of magnetic iron taconites, stage grinding and wet magnetic separation is standard practice. This also applies to iron ores of the non-magnetic type which after a reducing roast are amenable to magnetic separation. All such plants are large tonnage operations treating up to 50,000 …
The process flow of the extraction of iron from hematite is as follows: crushing, grinding, extracting (flotation separation, magnetic separation, gravity separation, etc.) and drying. Stage I Crushing and …
The haematite ore in South Africa is processed in a dry process to a HQ lump ore with 64 % iron content and a sintered fine ore with 63.5 % iron content. For fine ore beneficiation, wet processes are used. Capacity at the Minas Rio is to be increased from 26.5 Mta capacity to 28 Mta in the forthcoming years.
A novel low-intensity pneumatic planar magnetic separator designed to recover and concentrate fine-grained magnetite minerals is investigated and the …
Magnetic separation technology plays an important role in upgrading such low-grade iron ores, because the magnetic separation process possesses the combined advantages of large capacity and low operating cost, as well as being environmentally friendly. This chapter first introduces the principles and recent advances in magnetic …
Present investigation includes the magnetizing roasting of low-grade iron ore fines followed by grinding and beneficiation using magnetic separation. The hematite iron ore used in the investigation contains 53.17% T Fe, 10.7% SiO 2, and 4.5% Al 2 O 3. Powdered bituminous coal of 210 μm size with an ash content of 12.5% and fixed carbon …
testing uses state‑of‑the‑art iron ore beneficiation equipment for crushing, grinding, classification, gravity and electrostatic separation as well as high and low intensity magnetic separation for wet and dry applications. Our laboratory has the capability to create multi‑stage pilot scale circuits to treat bulk samples (80 ‑100
In the present study, iron ore feed with a size range of − 1 mm to + 0.1 mm with an assay of 58.28% Fe is subjected to dry processing on a thin/shallow bed air fluidized dry separator (TBAFDS). This unit is a gravity-based separator that utilizes the difference in minimum fluidization velocities of heavier and lighter particles.
The experimental results have shown that the FMS process is effective to recover hematite and limonite fines at a middle magnetic field intensity, greatly increased the separation efficiency, compared with the conventional magnetic separation at the same conditions. By applying the process to the fine hematite ore containing 30.5% Fe, …
In this paper, the properties, mineral magnetic modification, and beneficiation of tailings from the central mining and processing plant in Kryvyi Rih, Ukraine, have been studied. Samples were investigated by X-ray diffraction, X-ray fluorescence, microscopy, and magnetization measurements. The beneficiation was conducted using …
The magnetic susceptibilities of wüstite and fayalite are both considerably less than that of magnetite and hematite meaning that magnetic separation is not viable for the over-reduced samples. 3.3. Wet low-intensity magnetic separations (WLIMS) The work on dry beneficiation of iron ore minerals is limited and restricted to dry-magnetic ...
The trapped magnetic particles are easily washed out when the applied field is reduced to zero. Magnetic separators of this type are useful for the concentration or removal of fine magnetic particles when processing of iron ore for pellet feed. Magnetic separators are integral part of the low grade iron ore beneficiation systems.
Yu et al. used a process of magnetic reduction roasting followed by magnetic separation to separate and recover iron from a low-grade carbonatebearing iron ore, and the hematite and siderite ...
Abstract. Present investigation includes the magnetizing roasting of low-grade iron ore fines followed by grinding and beneficiation using magnetic separation. The hematite iron ore used in the investigation contains 53.17% T Fe, 10.7% SiO 2, and …
Finally, an iron ore concentrate assaying a Fe grade of 62.12% with a recovery of 56.93% was prepared using wet magnetic separation at a magnetic intensity of 0.5 T from the ore roasted under the ...
Abstract. In this paper, a sample from Tange-zagh iron mine was characterized by gravity and magnetic separation methods. The mineralogical studies …
Therefore, the generated waste iron ore beneficiation plant tailings (IOBPT) containing 56.96% Fe(T), 4.07% Al2O3, 7.23% SiO2 and 4.38% of LOI (contributed mainly from clay and goethite) can be ...
The most commonly used beneficiation methods for iron ores are the gravity and magnetic separation techniques [4−6]. Gravity separation is widely used in mineral …
Effect of feed size fraction on the concentrate assay and metal recovery using high intensity magnetic separator. The size labels are: 1 for - 500+20 μm, 2 for - 350+20 μm, and 3 for - 150+20 μm
In many iron ore mines, wet high-intensity magnetic separation is being preferred in the concentration of low-grade hematite ores to avoid the flotation methods. The other important factor is the selection of magnetic separator which can capture the hydroxyl-bearing iron minerals such as goethite and limonite that are feebly magnetic.
The investigations carried out on the low grade iron ore sample reveal the following conclusions. (1) The sample on average contains 43.8% Fe, 16.8% SiO 2 and 5.61% Al 2 O 3. (2) The mineralogical studies indicate that the major iron minerals are magnetite, hematite and goethite. And the gangue minerals are silicates and calcites.
1- The iron ores are considered as of low to moderate grade with respect to the iron. content (Fe O total is 42.08 - 47.58 %). 2- The ores are characterized by their high silica contents (28.85 ...
DOI: 10.1016/J.MINPRO.2017.09.012 Corpus ID: 102922119; Beneficiation of an iron ore fines by magnetization roasting and magnetic separation @article{Jianwen2017BeneficiationOA, title={Beneficiation of an iron ore fines by magnetization roasting and magnetic separation}, author={Yu Jianwen and Yue-xin …
Based on the obtained results by the investigation of the features of magnetite–hematite ores from the Mikhailovskoye deposit, a …
1. Introduction. High-intensity magnetic separation (HIMS) as an integral part of sorting paramagnetic materials has been widely used in different areas [1, 2], such as beneficiation of minerals [3], desulfurization of coal [4], non-metal ore purification [5], waste treatment [6], and nuclear fuel reprocessing [7].Over the span of decades, a …
Fig. 3 shows the magnetic separation process, which can successfully separate RE minerals and iron-bearing minerals. 55 Wang et al. 59 proposed a stepwise magnetic separation process to preconcentrate iron, RE minerals, and fluorite minerals from Bayan Obo ores. Their study adopted the superconducting magnetic separator …
On the other hand, oxidized iron ores like martite, hematite, specularite, limonite, and siderite are weakly magnetic, and require high-intensity and high gradient …
Magnetic Separation Principle. Magnetic separation is a beneficiation method that uses the magnetic difference between minerals in a non-uniform magnetic field to separate different minerals. Magnetic separation is the most commonly used beneficiation method for ferrous metal ore such as iron ore. It is divided into weak …
حقوق النشر © 2024.Artom كل الحقوق محفوظة.خريطة الموقع