Energy-saving and Efficient Vertical Roller Mill | Fote …
The structure of the vertical milling machine is mainly composed of the grinding roller, grinding table, separator, rocker arm, gearbox, stand, hydraulic system, and other parts. The following are key parts of the vertical mill: 1. Grinding roller. Grinding rollers (usually 2–4) are the heart of the vertical mill, distributed on the grinding ...
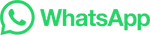