Zinc processing | Extraction, Refining & Uses
The Zinc Mining Process. The zinc mining process is conducted primarily underground, with more than 80 percent of all zinc …
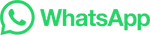
The Zinc Mining Process. The zinc mining process is conducted primarily underground, with more than 80 percent of all zinc …
Lead. A. Mohamad Ghazi, James R. Millette, in Environmental Forensics, 1964. 4.3.2 Mining and Production of Lead. Lead and zinc ores often occur together, and there are a large number of countries that mine and process lead ore, making it among the most widespread metals in terms of primary production (Kesler, 1994).Most of lead mining is …
Mining wastes include waste generated during the extraction, beneficiation, and processing of minerals. Most extraction and beneficiation wastes from hardrock mining (the mining of metallic ores and phosphate rock) and 20 specific mineral processing wastes (see side bar below) are categorized by EPA as "special wastes" and have been exempted by ...
Final Product: The end result of the processing and refining of cadmium ore is high-purity cadmium metal, ready for use in various industrial applications. Throughout the entire processing and refining process, strict safety protocols and environmental regulations must be followed to ensure the safety of workers, protect the environment, …
Garnet Mining process, how to extract mineral from rock and placer deposit, related processing plant flow chart and layout design. read more. ... In China, hard-rock mining may consist of more primitive methods including hand mining. Garnets are extracted and processed more easily from alluvial deposits. For example, at the Emerald Creek mine ...
The 5 Lifecycle Stages of Mining. 1. Exploration & Prospecting Stage. This is the first and most essential step of the mining process: in order to open a mine, companies must first find an economically sufficient amount of the deposit (an amount of ore or mineral that makes exploitation worthwhile.) Geologists are enlisted by the companies to ...
Zinc mining process. More than 80% of zinc is extracted from underground mines. 8% of zinc is mined in open pits, while the remaining 12% is mined by these two methods. Once removed from the soil, the concentrate is baked at a temperature of 950 degrees Celsius, which oxidizes zinc, sulfur and iron. The zinc and iron oxides will be …
Flowchart of zinc concentrate production ResearchGate. Zinc and lead metal production processes also have high energy requirements and produce CO 2 at the mining and beneficiation stages (Tao et al 2019) For example, the primary process ofZinc content allocation ensures that the final zinccontaining products have an accurate value for …
Mining and concentrating. Zinc ores are recovered by many mining techniques, ranging from open-pit mining (mainly in the case of oxidized ore bodies, which are located closer …
Significant amounts of lead are recovered as a by-product or co-product from zinc mines, and silver-copper deposits. Primary refined lead was produced at one smelter-refinery in Missouri. Of the plants that produced secondary lead at year end 2013, 12 had capacities of 30,000 tons per year of refined lead or greater and accounted for more than ...
It has an ore production capacity of 6.15 million MT per annum, with best-in-class zinc-lead reserves grade of 15.8%. It produced 528,459 MT of mined metal in the year FY 2017. Reserve and resource of Rampura Agucha Mine as on 31st March 2017 are 100 million MT. Rampura Agucha operations include both open pit and underground mining.
Zinc ores normally contain 5–15% zinc. Approximately 80% of zinc mines are underground mined, 8% are mined from open pits, and the remainder are a combination of both ores ( Ray et al., 2014 ). Zinc concentrate, which contains approximately 55% zinc, is roasted at a temperature approximately 800°C (1472°F).
The eight groups of minerals commodities selected include: Coal; Potash, Soda Ash, and Borate; Iron; Copper; Lead and Zinc; Gold and Silver; Phosphate Rock, and Crushed Rock. These commodities represent 66 percent of all production value in mining in the U.S. Although energy data are withheld for a number of mined commodities, the commodities ...
The reaction involved in the final step of extraction of zinc is: [ZnO + C rightarrow Zn + CO] Purification: The last step involves the purification of Zinc, Zinc is …
Non-ferrous metal minerals resources are indispensable and play an important role in economic development [].In the process of the exploitation of mineral resources, a large amount of mining waste rock has been produced [].According to the report on National Mineral Resources Conservation and Comprehensive Utilization …
R. U. Ayres et al The life cycle of copper, its co-products and byproducts v TABLES .....147 Table 1.1: Accumulated use of metals compared to various measures of future
Zinc is essential in producing numerous products, from galvanizing steel to creating brass alloys. Making zinc metal from ore can be broken down into three steps: mining, smelting, and refining. This …
The principal ore of zinc used for its extraction is Zinc blend ( Z n S). As Zinc blend is a sulphide ore, the process used for its concentration is the Froth Floatation Method. The concentrated ore is …
Malvern Panalytical delivers innovative and unique mineral analysis solutions to increase the efficiency of your mining operation. Our robust and reliable systems, expertise and support help in all steps of your mining process, from exploration to the analysis of final products. احصل على السعر
Silica Sand Mining introduces. Foundry silica sand is the quartz as the main mineral composition, particle size of 0.020 mm to 3.350 mm refractory particles, according to the mining and processing methods of different can be divided into artificial silica sand and sand washing, sand washing, selection of natural silica sand such as sand (flotation).
Zinc Ore Crusher Machinery, Zinc Mining Processing Plant …. Zinc ore mining process can supply many products to industry. For Zinc ore mining, miners … transferred to underground rock … maximum particle size of the final product … » Free Online Chat Zinc – Wikipedia, the free encyclopedia. A final concentration of zinc of about 50% is …
The gold mining operation stage represents the productive life of a gold mine, during which ore is extracted and processed into gold. Processing gold involves transforming rock and ore into a metallic alloy of substantial purity – known as doré – typically containing between 60-90% gold. During its life, a number of factors – such as the ...
Zinc ore refers to the naturally occurring rock or mineral that contains a significant concentration of zinc. Zinc is a chemical element with the symbol Zn and atomic number 30. It is a bluish-white, lustrous metal that is known for its excellent corrosion resistance, malleability, and conductivity. Zinc is an important industrial metal used in …
The reaction involved in the final step of extraction of zinc is: ZnO + C → Zn + CO Z n O + C → Z n + C O. Purification: The last step involves the purification of Zinc, Zinc is purified by electrolytic refining. In this process, impure zinc is anode and cathode is of a pure thin sheet of zinc and the electrolyte used is.
This post has outlined the main zinc production process for producing pure and its alloys. Zinc processing is the process of extracting zinc from its ores for use in different products. Because of the low melting point of 788 °F (420 °C), pure zinc applications are not many. However, alloyed forms have very many applications.
3 Environmental and human impact. • Either of the two zinc production and refining stages outweigh the mining and mineral processing. • The Hydrometallurgical Process produces high levels of liquid waste and is …
Zinc is mined using different methods such as open-pit mining (for the case of oxidized ores) and underground mining methods (for the case of sulfide ores). The …
zinc mining and processing methods from rock to concentrate. 09-09-2019· Zinc concentrate is produced by separating the ore, which may contain as little as 2% zinc, from waste rock by crushing and flotation, a process normally performed at the mining site. The zinc concentrate is then reduced to zinc metal in one of two ways either ...
lead zinc processing Plant. 10TPH lead zinc flotation process plant, the main equipment including: 1. Crushing & screening: Excavators or loaders send materials into the raw ore bin, and feed them to the jaw crusher …
The mining process generates a significant quantity of waste materials that must be operated strategically to balance economic productivity with environmental sustainability. ... Synthetic cryolite can be recovered as a by-product in phosphate rock processing and alumina manufacture. d. Nickel: The technology so developed pave the …
حقوق النشر © 2024.Artom كل الحقوق محفوظة.خريطة الموقع