Grinding Kaolin Clay? Now Is the Time to Know the Best Way
Kaolin ultrafine mill is a kind of fine grinding equipment with a more scientific and reasonable process. It is used for the efficient processing of ultrafine kaolin powder. Features: Price: $2,000 / set (the lowest price) Maximum feed size: ≤40mm. Production capacity: 0.8-25t/h. Finished product fineness: 60-800 mesh.
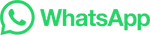