Crusher
Crushers are widely used as a primary stage to produce the particulate product finer than about 50–100 mm in size. They are classified as jaw, gyratory and cone crushers based …
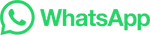
Crushers are widely used as a primary stage to produce the particulate product finer than about 50–100 mm in size. They are classified as jaw, gyratory and cone crushers based …
Jaw Crusher. This type of primary crusher is usually used for crushing shale to reduce it to a size suitable for handling. Roll Crusher. For a given reduction ratio, single-roll crushers are capable of reducing ROM material to a product with a top size in the range of 200–18 mm in a single pass, depending upon the top size of the feed coal ...
Relation between Feed size and Shape. The greater reduction ratio the worse particle shape. Inter particle breakage improves shape. When crushing a bed of material …
Crusher safety starts with the person feeding the plant. This person needs to be trained on crusher best practices specific to the machine they are working with. An operator may have years of experience of operating and loading a cone crusher, but that does not translate into experience of loading and operating a jaw crusher.
The results of the analysis in 200 h operating interval show that the probability of failure occurrence for crushing, conveyor systems, crushing and mixing bed hall department is 73, 64, and 95 percent respectively and the conveyor belt subsystem found as the most probable system for failure. Finally, maintenance as a method of control and ...
A prototype was constructed to evaluat e the design analysis carried out. Rock crushing machines are highly essential in the mineral processing and . ... In a crusher machine, where the operation ...
This study reports on the design optimisation of the swinging jaw crusher plate. Jaw crusher machines are used in the mining and construction industry for crushing rocks and mineral ores to the ...
Abstract: Crushers are major size reduction equipment used in mechanical, metallurgical and allied industries which crushes different types of soft and hard materials. swing jaw plates are takes direct part into this oprations.hence the design and analysis are very important .This paper focuses on review of a work carried out by researchers on …
Fig -8: Crushing strength variation with mass of Crusher It is quite evident from the analysis that as the mass of the crusher increases the crushing strength of the aluminium can decreases that is the load required to totally …
of the machine in the market, the completion of the new model provides a more practical usage than ... mechanism and forces analysis are increased. In order to reduce the waste, we planned to create a can crushing machine that will reduce the volume of aluminum cans by approximate eighty percent. This machine primarily usage …
A rock crusher is an industrial machine used to break rocks into smaller pieces by using a rotating or reciprocating motion. The smaller pieces are then easier to handle and can be put into different types of products, such as gravel, sand, and dust. The main production cost for a rock crusher is the cost of the machinery itself, while the cost ...
software, and Modal analysis was performed by using ANSYS Workbench 19.2. Keywords Crush of stone ·FE model ·Frequencies ·Deflections 1 Introduction In industries, crushers [1] and machines which use tools to break or compress mate-rials into small fractional chunks or denser masses are known as crushers. At the
This paper presents experimental comparison of two machine crushing technologies: one-stage and two-stage. The study was carried on a model double-toggle jaw crusher which allows crushing forces ...
The corresponding DEM analysis model of the gyratory crusher is established in this paper by referring to the relevant parameters of the Superior MKIII 60–110 coarse crushing gyratory crusher (, 2022, Shi and Kojovic, 2007) manufactured by , as shown in Fig. 4. Its closed side setting is 203 mm.
During the operation of a forage crusher, the common issues usually faced are shorter mean time between failures and low reliability. The hammer rotor, a critical component, is prone to fatigue fracture, hammer wear, violent vibration of the rotor system caused by uneven wear of the hammers, and other issues that reduce the machine's …
CRUSHER..Ph..0475 217 533..Risk and Hazard Assessment is the identification of risks and hazards associated with the CRUSHER. Compliant Industries Group hazard and risk assessors are experienced on the plant and will go through every aspect of your CRUSHER in a thorough process.
1.2 The jaw crusher. Crushing is the first stage of size reduction of mined rocks. Primary crushers are heavy-duty machines, used to reduce the run-of-mine (ROM) ore down to a size suitable for easy handling. A line diagram of a double toggle jaw crusher and its main components is shown in figure 2. The jaws are set at an angle to each other.
Plant dynamics is a complex phenomenon where correlation and casualization can be vague. To simulate plant dynamics mathematical models for every production unit, e.g. crushers, screens, conveyors, silos, etc., has to be created. The models describe the changes in flow and particle size of the material traveling through the plant.
This paper describes about the experimentation of can or plastic bottle crusher machine and analysis of mechanism used in machine. ... The manufacturing cost as well as the maintenance cost is very less as compared to that of hydraulic machines. This crusher can crush the waste effectively and also the operating time is very less as compared to ...
1. Twin roll crusher. 2. Cone crusher. 3. Vertical Shaft Impactor (VSI) These show the nature and level of fidelity that is now possible to include in particle scale …
The Automatic Can. Crusher is run by a Programmable Logic Controller (PLC) with the aid of an. inductive and capacitive sensor, where it is applied to detect whether the. object is metal or non ...
We can conclude that plastic is crushed with the help of a plastic crushing machine hence we also design and manufacture plastic crushing machines. Plastic is an essential part of our day-to-day life. ... Comparative Analysis of Plastic Bottle Crusher Machine: A review Sthageeta Nilkanth Chiwande1, Dr. M. Sohail Pervez. [2] Mr. Shadab Husain ...
As experience shows, when one determines the energy-power parameters of crushing and grinding processes by using the existing methods, the power of motors used in drives of existing crushers of various types often turns out to be excessive [10, 11].In this case, the drive will operate at a relatively low load (ratio of the power consumed by the …
So the design of this machine will intend to fill this demand. So our main objective of the project is to design the impact stone crusher. 2 DESIGN METHODOLOGY Defining the problem and gathering information regarding the crushing machine. Surveying different literature (journals and books) about the stone crusher machine [4]. IJSER Fig. 2.
This paper describes about the experimentation of can or plastic bottle crusher machine and analysis of mechanism used in machine. Hence in this the knowledge of analysis is necessary, and by analysis of various parts the quality and life of machine ... Crushing is the process of transferring a force amplified by mechanical advantage through a ...
A is a device to reduce large material object into a smaller volume. The crusher reduces the size or change the form of waste materials so that they can be disposed off or recycled easily. The Can …
For the 1-in. screen below the roll crusher the capacity has no correction factor and the area needed is 32/2.1 = 15.2 sq ft. To handle the output from a 40 x 24 roll crusher the screen will have to be at least 24 in. wide. Perhaps it will be more effective to use one continuous screen of at least 20.1 + 15.2 = 35.3 sq ft.
Failure analysis of a crusher jaw. John O. Olawale, Simeon A. Ibitoye, in Handbook of Materials Failure Analysis, 2018. 1. Introduction. Crusher machines are used for crushing of a wide variety of materials in the mining, iron and steel, and quarry industries. In quarry industry, they are used for crushing of rocks into granites for road ...
Performance analysis was carried out on the plastic crushing machine and the efficiency was calculated as 85.16% while the average machine through put capacity was determined as 0.112kg/sec ...
The difference between the cumulative percentages at the 3.5″ and 1.5″ points on the curve gives us the amount, of such product to be expected from the output of the primary crusher This is 85 minus 43, or 42% of the primary crusher product. If our problem had covered a crushing condition calling for 80 instead of 85% passing the …
حقوق النشر © 2024.Artom كل الحقوق محفوظة.خريطة الموقع