(PDF) Utilization of low-grade BHQ iron ore by …
Keywords: reduction roasting process / iron ore / banded hematite quartzite / BHQ / hematite / magnetite / goethite / non-coking coal / magnetic separation / pelletization 1 Introduction
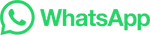
Keywords: reduction roasting process / iron ore / banded hematite quartzite / BHQ / hematite / magnetite / goethite / non-coking coal / magnetic separation / pelletization 1 Introduction
Magnetic separation is the mineral separation method to separate different minerals by magnetic differences. Basic Principle. Based on the level of …
Magnetization roasting followed by magnetic separation is considered an effective method for recovering iron minerals. As hematite and magnetite are the main concomitant constituents in iron ores, the separation index after the magnetization roasting will be more optimized than with only hematite. In this research, the mechanism of the …
The iron oxide mineral magnetite as Fe 3 O 4 has a mass percent of 72.36% Fe and 27.64% O and typically occurs as a natural ore containing 15–40% Fe. Historically hematite direct shipping ore (DSO) has been the preferred source of iron ore globally, with significant resources located on several continents, including Australia in the Hamersley …
The fine ore from the underflow is sent on the other hand to a spiral classifier, where density separation of the metal ore and gangue taking place in several stages. ... CITIC Pacific Mining had put into operation a first line from a total of six for the production of a magnetite iron ore concentrate in the Pilbara region. The capacity of the ...
In this paper, a sample from Tange-zagh iron mine was characterized by gravity and magnetic separation methods. The mineralogical studies showed that hematite and goethite are the main iron-bearing minerals with insignificant amounts of FeO. The results indicated that spiral separation yields higher separation efficiency than …
Abstract: Conventional magnetic separation devices are widely used for the removal of tramp iron from a variety of feed materials and for the beneficiation of ferrous ores. …
Wet magnetic separation is the main beneficiation process at iron ore enterprises in Russia and abroad. Conventional magnetite ore processing flowcharts …
Diseño de Procesos de Conminución Eco-. Eficientes y Reducción de Costos para. Mineral de Hierro Magnetita. Eco-Efficient and Cost-Effective Process. Design for Magnetite Iron Ore. Alex ...
Magnetization roasting followed by magnetic separation is considered an effective method for recovering iron minerals. As hematite and magnetite are the main …
Considering that the low-grade iron ore resources account for 97.5% of the total reserves in China (Zhang et al., 2020), the exploitation and utilization of low-grade magnetite ore resources have become vital and urgent issues to realize the sustainable development of China's iron and steel industry (Deng et al., 2020, Zong et al., 2018).
Dwari et al. (2013) used a combination of dry and wet magnetic separation methods to upgrade a low-grade siliceous iron ore with magnetite, hematite, and goethite as major iron minerals. The study showed that for particles finer than 200 µm, the separation methods produced a magnetic concentrate with 67% iron and iron recovery …
In this paper, the beneficiation of a low-grade hematite ore fines containing carbonates with magnetization roasting and magnetic separation was proposed and studied. The hematite and siderite are almost completely converted into magnetite by 8 wt% coal at roasting temperature of 800 °C for 8 min.
The largest development in the iron-ore industry, using magnetic concentration, is at the plants of Witherbee, Sherman & Co. at Mineville, N. Y., where about 1,200,000 tons of crude ore were mined …
To determine the phase composition of iron minerals in the raw ore, iron phase analysis of the ore was performed, and the results are presented in Table 2.It can be observed from Table 2 that the iron in the ore occurred primarily in magnetite with a content of 51.97%. The total amount of iron in the hematite, iron carbonate, pyrite, and …
Materials Science. Magnetite. Chapter. Physical separation of iron ore: magnetic separation. January 2022. DOI: 10.1016/B978-0-12-820226-5.00010-0. In …
South African vanadium–titanium magnetite is a complex mineral resource rich in iron, vanadium, titanium, and chromium [1,2,3].Its ore composition is composed of more than 20 elements [4,5,6].It is the most complex ore of its type in the world and contains more than 10 valuable elements, so it has a very important integrated utilization …
Dry magnetic separation (DMS) enables to separate the non-magnetic fraction of iron ores at the initial stage of their concentration and therefore to decrease cost of their …
The separation technology provides for production of iron ore concentrate with total iron content of 65.9% and recovers 91.0% of magnetite and 80.5% of hematite from the tailings containing 20.4% ...
1. Introduction. Iron is one of the most abundant elements in the earth's crust. It always coexists with metals in the ore, mainly exists in the form of hematite, magnetite and muscovite on the surface of particles or in the inclusions inside crystals [].In hydrometallurgy, iron, although is converted into insoluble precipitates and removed in …
Iron ores such as hematite, magnetite, and limonite are also used in cosmetics, paint, medicine, ... Moreover, Mn grades of these concentrates were below 2.35% allowing the magnetic product to be classified as salable iron ore products. Magnetic separation test results found in the literature support the findings of this study [72,73,74].
Use of Magnetite as an Ore of Iron. Most of the iron ore mined today is a banded sedimentary rock known as taconite that contains a mixture of magnetite, hematite, and chert. Once considered a waste material, taconite became an important ore after higher grade deposits were depleted. Today's commercial taconites contain 25 to 30% iron by …
Dry magnetic separation is a technology that sorts magnetic minerals from gangue using air as the medium instead of water. When raw ore is fed to the magnetic separator, the magnetic particles are subjected …
The ore is roasted under reducing conditions to selectively reduce iron. The iron is then removed by magnetic separation, and the non-magnetic material leached in hydrochloric acid. This process also enables the recovery of a titanium dioxide by-product (Zhao et al., 2014). The production of by-products such as titanium dioxide, iron metal or ...
Effect of magnetic intensity on separation of vanadium, titanium and iron. In this study, magnetic separation was used to obtain high-quality vanadium concentrates from the VTM ore. The production of titanium-rich concentrates to recover titanium was also very important because the VTM ore contains high ilmenite [26, 27]. Therefore, from the ...
This chapter introduces the principle of how low-grade iron ores are upgraded to high-quality iron ore concentrates by magnetic separation. Magnetite is the most magnetic of all the naturally occurring minerals on earth, so low-intensity magnetic …
Obtaining high-quality concentrates with high iron content and low content of impurities from low-grade iron ores requires the …
Iron concentrations greater than 69%, and SiO2 concentrations less than 2% with overall magnetite recoveries greater than 67% and 71% were obtained for zones 1 and 2, respectively. Keywords: magnetite; flotation; magnetic separation; starch; amines 1. Introduction The demand for high-grade magnetite in the iron and
If properly implemented, this new separation system can eliminate iron contamination and provide coal that can be marketed as a high-quality silicon feedstock. ... Iron ore tailing—a waste material of mineral beneficiation plants, is used as a source of iron for synthesizing magnetite powder. Iron ore tailings containing 15.98% Fe 2 O 3, ...
problem in iron ore smelting process. However, the magnetic separation of pyrrhotite from magnetite is problematic, due to their similar magnetic property and magnetic flocculation between pyrrhotite and magnetite [3]. Flotation has been commercially used as a method for removing pyrrhotite from magnetite for high sulfurous iron ores [4].
حقوق النشر © 2024.Artom كل الحقوق محفوظة.خريطة الموقع