Challenges in processing nickel laterite ores by flotation
Only ultrafine grinding will liberate nickel and cobalt in very fine particles, the recovery of which is relatively low in conventional flotation cells (Farrokhpay and Filippov, 2016 ...
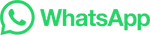
Only ultrafine grinding will liberate nickel and cobalt in very fine particles, the recovery of which is relatively low in conventional flotation cells (Farrokhpay and Filippov, 2016 ...
The rougher flotation and closed-circuit flotation tests of copper-nickel sulfide ore (1.0 kg) were performed on XFD-63 type flotation machines of different capacities (3.0 L, 1.0 L, obtained from Wuhan Exploration Machinery Co., Ltd.) [5], with mechanically stirring speed of 1610 rpm.The 3.0 L cell was used for rougher and scavenger stages, and the 1.0 L …
A flotation testing program on nickel ore with an important degree of oxidation should evaluate the effect of sulphidization. The typical reagent is NaHS. The collector is a xanthate, Potassium Amyl Xanthate (PAX) is a strong collector. MIBC or Dowfroth 250 can be evaluate as frother.
In flotation plants, lime additions are common in different points of the circuit, such as comminution (crushing and grinding), flotation, and dewatering/thickening. ... Xu, M., 2016. Method for improving selectivity and recovery in the flotation of nickel sulphide ores that contain pyrrhotite by exploiting the synergy of multiple depressants ...
Most of the world's nickel is extracted from the mineral pentlandite, (Ni, Fe)9S8, which frequently oc-curs in ores containing predominantly pyrrhotite and various non-sulRdes, …
Nickel smelting slag contains valuable metals including nickel and copper. Failure to recycle these metals wastes resources, and disposal of nickel slag in stockpiles results in environmental pollution. Nickel slag recycling is important, and metals can be recovered from slag by flotation. However, considering the complex forms in which …
Flotation. According to the difference in physicochemical properties of mineral particle surfaces, flotation is the method that selectively enriches the target minerals in the pulp at the gas-liquid interface and separates them from the pulp, thus realizing the mineral separation. It is also known as floating separation.
Abstract. Effect of calcium and thiosulfate ions on flotation of a Ni–Cu ore was investigated. The ions improved the flotability of sulfides at the normal process pH after grinding in steel mill ...
Effect of calcium and thiosulfate ions on flotation of a Ni–Cu ore was investigated. The ions improved the flotability of sulfides at the normal process pH after grinding in steel mill. Calcium activated especially nickel and copper sulfides when the galvanic effect of mill iron was effective. The UV/Vis measurements showed that calcium …
A novel method of cryogenic grinding and froth flotation is proposed to recover LiCoO 2 and graphite from spent lithium-ion batteries. After 9 min of cryogenic grinding, the grade of LiCoO 2 concentrate was up to 91.75%, with a recovery rate of 89.83% after flotation, but the materials that have not been cryogenic grinding, the …
The flotation behavior of beryl and spodumene (typical silicate minerals) was studied at wet-grinding conditions with different grinding mediums, with dodecylamine or sodium oleate as the collector. The mechanism of potential influence of the grinding medium to the flotation behavior was investigated through measuring zeta potential of …
This paper presents the findings of a flotation study to recover awaruite from the Baptiste ultramafic deposit, located in central British Columbia, Canada. Nickel recoveries of up to 65% at the rougher stage were obtained with xanthate as a collector at a pH level of 4.5. Awaruite flotation was shown to be highly dependent on the slurry pH.
A nickel-copper sulfide system usually coexists with serpentine in deposits. Low nickel-copper recovery and high content of serpentine in concentration adversely affects subsequent metallurgical processes. In this study, test data showed different rheological results at various densities. When the solid ratio of sulfide to serpentine was …
Grinding The procedure adopted in all tests was to grind 50 g of gersdorffite with 450 g of quartz and 250 ml of either distilled water or deoxygenated distilled water (pulp density of 67% solids) at natural pH (pH 6.8). The grinding mill was a closed iron mill (23 cm diameter by 20 cm long) with a 4 kg charge of 25 mm mild steel balls.
The lizardite breaks readily during the grinding process and produces slimes, which are positively charged at the pH where flotation of nickel sulphide ore is performed. Thus the slime will adsorb onto the negatively charged pentlandite surface through electrostatic attraction and depress pentlandite flotation.
involving pentlandite, chalcopyrite, pyrrhOlite, pyrite and grinding media and a mechanism has been pr
Literature shows that flotation has not been successful to recover nickel from laterite ores. Nickel in laterite ores is often finely disseminated in various minerals …
Ore mineralogy of nickel laterites: controls on processing characteristics under simulated heap-leach conditions. The mineral phases in more than 50 Ni laterite ores were determined before and after the ores were acid-leached in columns for more than 120 days. The selected ore samples have wide variations in….
Vezina (Citation 1973) studied the pressure oxidation of a Canadian copper–nickel flotation concentrate grading 6.85% Ni, 8.83% Cu and 0.55% Co under a variety of conditions (refer ... Wet grinding for 30 min in a planetary mill followed by leaching at ambient pressure for 2 h resulted in close to extraction of Ni from the ...
Section snippets Materials and reagents. The pentlandite ore sample with 0.58% Ni was crushed to a size of −2.36 mm before grinding and flotation.Mineralogy analysis shows that pentlandite was the main nickel mineral with small amounts of millerite, violarite and heazlewoodite while chrysotile, antigorite and lizardite were the main …
Grinding and Flotation. Fine ore at minus 19mm (¾") sizing is fed at a controlled rate into the open-circuit 2600mm x 3960mm (8'-6 x 13'-0) Hardinge rod mill at an average feed rate of 2,106 STPD or 87.75 …
1. Introduction. Wet milling in ball mills followed by flotation is the general practice employed in the beneficiation of copper sulphide ores in which the major minerals of commercial significance typically are chalcopyrite (CuFeS 2), bornite (Cu 5 FeS 4), covellite (CuS) and chalcocite (Cu 2 S). The flotation response of ground minerals can …
• Grinding • Flotation Leaching: • Nickel matte sulfate leaching • Nickel matte chloride leaching • Nickel concentrate sulfate leaching • Nickel concentrate chloride leaching • …
The present study initially investigates the kinetics of microwave-assisted grinding and flotation in a porphyry copper deposit. Kinetic tests were conducted on untreated and microwave-irradiated samples by varying the exposure time from 15 to 150 s. Optical microscopy, energy-dispersive X-ray spectroscopy, and scanning electron …
Froth flotation has been the most widely used approach for treating complex low-grade and finely disseminated ores. Flotation pulp consists of micro-particles with a certain grinding fineness, which is generally expressed as the mass ratio (%) of less than 0.074 mm/the total grinding product (the grinding fineness depends on the target …
• Grinding • Flotation Leaching: • Nickel matte sulfate leaching • Nickel matte chloride leaching • Nickel concentrate sulfate leaching ... nickel and cobalt sulfate crystals are dissolved to form a purified metal sulfate solution from which the cathode precursor manufacturing starts.
The final tailing was rejected in the cobalt-nickel circuit. The flotation pilot plant is shown. Results typical of a single shift during the pilot run are summarized. The recoveries of lead and copper were 87.1% and …
Product: Oxfloat D100 is of the CMC family of depressant. With the purpose of MgO Depression, this is commonly used in Southern Africa for Talc depression in PGM/Nickel flotation circuits. Also known as SODIUM CARBOXYMETHYL CELLULOSE Preparation: Make 0.5% solution in water. Add product to water into stirred beaker to …
The conventional nickel ore beneficiation process is divided into four stages: crushing & screening, grinding & grading, flotation, dehydration & drying. 1. Crushing & Screening. The raw ore enters the jaw crusher through the feeder for primary crushing and then enters the cone crusher for medium crushing.
In order to simulate and predict the surface topography of nickel-base superalloy processed by electroplated grinding head, a digital modeling method of electroplated grinding head was proposed, which considered three key factors: abrasive shape, abrasive spacing and abrasive height. The whole digital model of electroplated …
حقوق النشر © 2024.Artom كل الحقوق محفوظة.خريطة الموقع