mill/sbm hematite iron ore processing sbm mobile crusher…
Contribute to crush2022/mill development by creating an account on GitHub.
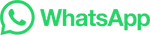
Contribute to crush2022/mill development by creating an account on GitHub.
Here's an overview of the equipment commonly used in hematite grinding and iron ore processing: 1. **Crushing Equipment**: - ** Jaw Crusher **: Used for the primary crushing of hematite ore, reducing the ore size to approximately 20-40 mm. - ** Cone …
Hematite is a kind of iron oxide ore, the main component is Fe2O3, it is dark red, the specific gravity is about 5.26, and it contains 70% Fe and 30% O. ... and hammer crushing or cone crushing is selected for the fine crushing process according to the situation. The crushed materials enter the circular vibrating screen for screening, and the ...
This paper mainly highlights the formation of magnetite ore (Fe 3 O 4) by reduction of hematite iron ore (Fe 2 O ). Here, Fe and Fe 3 O 4 are magnetic, while FeO and Fe 2 O 3 are non-magnetic in nature. 2. MATERIALS AND METHODOLOGY EMPLOYED IN THE STUDY 2.1. Materials. A sample of low-grade hematite iron ore was obtained from the …
The former mainly selects magnetite ore, and the latter is mainly used for sorting hematite, mixed iron ore and weak magnetic ore. 6.2 Magnetic separation – cation reverse flotation process The grade of …
1. flotation separation. The flotation method is mainly used to separate fine-grained and particulate weak magnetic hematite ore, including two processes: positive …
Jaw Crusher impactors are designed for crushing hard to soft materials like limestone, iron ore, coal etc. These impactors are available in various sizes ranging from 400 mm to 1200 mm diameter and width upto 2000 mm. Star trace can offer duty impactors, specially designed for coal and similar materials.
The picture above is a hematite ore processing site in Xinjiang, the hematite ore processing plant uses jaw crusher coarse crushing, cone crusher fine crushing, vibrating screen screening, trapezoidal jigger gravity separation, dewatering screen dewatering, a total of 4 hematite ore processing production lines designed and …
Also be called iron ore beneficiation equipment, the hematite ore beneficiation equipment consists of crushing equipment, grinding machine, fine particle screening and grading equipment, magnetic …
There are two main types of hematite gravity separation methods: coarse-grain gravity separation and fine-grain gravity separation: Coarse-grain gravity separation: the geological grade of the deposit is high (about 50%), but the ore body is thin or there are many interlayers, and the waste rock is mixed in during mining to deplete the ore.For this …
Nowadays, hematite iron ore processing has been a large demand of iron ore plant owner, many hematite iron ore processing plants would consult peers on the website about which manufacturer is the best choice for extraction of iron from hematite? Xinhai is your best choice. Xinhai majors in manufacturing hematite iron ore …
Impact Crushers. The impact crusher, also known as the impactor or horizontal shaft impact crusher, is a equipment that uses impact energy to crush medium-hardness brittle materials finely. Commonly used in various applications including construction, mining and recycling. Impact mills can produce a high-quality cubic end product.
Table of Contents The authors investigate the influence of the basicity index CaO/SiO2 on the sintering properties of hematite ore mixtures. The experimentation was performed with three different mixtures of ores from Tazadit, Nimba, Mano-River, Itabira, Marcona, Goa, Mapawa and Cassinga. Increasing the basicity index CaO/SiO2 between …
Abstract. Hematite and magnetite, the two predominant iron ores, require different processing routes. High-grade hematite direct shipping ores (DSOs) generally …
Hematite Iron ore mobile crusher arrives based on novel collection iron ore crushing equipment's agreement idea, which expands this field of coarse mashing and fine … Mobile Iron Ore Processing Equipment – Stone Crushing Machine
The three-stage open circuit process is used to process argillaceous iron ore with high water content and large and medium-sized iron ore concentrators that are prone to produce a large amount of quartz dust ore. Its advantage is that it can simplify the equipment configuration of the crushing workshop and reduce the capital construction ...
Iron ore Processing Plant. At present, there are about 300 kinds of iron-bearing minerals found in nature. According to the classification of chemical composition, the common iron ore mainly includes magnetite, hematite, limonite and siderite. Different properties of iron ore, its processing technology is naturally different.
The raw ore contains 42% iron. The hematite is easily separated from the gangue and enters the jigger for gravity beneficiation after crushing and screening. After washing, jigging, and spiral beneficiation of this type of hematite ore, 49% of the mixed concentrate is obtained, with a recovery rate of over 90%.
The iron itself is usually found in the form of magnetite, hematite, goethite, limonite or siderite. PROCESSING TECHING. The crushing and dry separation of iron ore should follow the principle of lowest operation cost. The cost accounting needs to be done before the new project. The key equipment should have high efficient leaving out the ...
Hematite mineral processing equipment as follows: Crushing equipment: jaw crusher, impact crusher, cone crusher. Jaw crusher to coarse jaw broken and sucked jaw broken. Ground mining equipment: cone ball mill, ceramic ball mill, energy-saving ball mill, high-energy ball mill, high fine ball mill. Fine sieving and grading equipment: grader, air ...
Aug 23, 2019 The former mainly selects magnetite ore, and the latter is mainly used for sorting hematite, mixed iron ore and weak magnetic ore. 6.2 Magnetic separation – cation reverse flotation process The grade of iron concentrate increased from 65.55% to 38.89%, the silica content decreased from 8.31% to 3.90%, and the iron recovery rate ...
The iron ore processing industry produces usable concentrations of iron-bearing material by removing nonferrous rock (gangue) from low-grade ore. In the United States, predominant iron ore is taconite which is a hard, banded, low-grade ore. Ninety-nine percent of the crude iron ore produced in the United States is taconite.
Also known as red hematite ore of its chemical formula is Fe2O3, which is a weakly magnetic iron minerals, magnetite floatability than good, one of the main raw material is iron. The main mineral processing technology have re-election, and strong magnetic separation or flotation process and use a variety of mineral, and there have been post …
Hematite: Dry process, crushing & screening (two stage) followed by blending: 8. Rajhara, Durg (Chhattisgarh) Hematite: Dry process, crushing & …
Firstly, the raw hematite ores are evenly sent to a jaw crusher through a vibrating feeder for coarse crushing, then are sent to a cone crusher for fine crushing. Next, the ore is screened by a vibrating screen. Those whose particle size meet the requirements would be sent for grinding, while the others would return the cone cr…See more on ftmmachinery
WEBHematite and magnetite, the two predominant iron ores, require different processing routes. High-grade hematite direct shipping ores generally only require …
Luster. Metallic. Iron ore beneficiation process. The iron-rich ore that can be directly into the furnace in China only accounts for 2.6% of the total reserves. There are many types of lean iron ore, …
hematite ore crushing plant processing. Hematite Iron ore crushing and screening plant can also be called mobile iron ore crusher and may be the portable complete …
Magnetite. Karara comprises a large-scale, long-life magnetite orebody amenable to bulk mining and processing. Magnetite ore has lower iron content (34-36% Fe) than hematite ore (58-64% Fe). It must be upgraded by a complex ore treatment process (beneficiation) to produce a high-grade (+65% Fe) concentrate for steelmaking.
The six main steps of iron ore processing - Multotec. Six steps to process iron ore 1. Screening We recommend that you begin by screening the iron ore to separate fine particles below the crusher's CSS before the crushing stage. A . Obtener precio 8 - Developments in iron ore comminution and. 2015.1.1 Crushing Processing Mills Stirred …
The partially reduced ore is then smelted in the second unit, and liquid iron is produced. Smelting-reduction technology enables a wide range of coals to be used for iron making. Iron processing - Ores, Smelting, Refining: Iron ores occur in igneous, metamorphic (transformed), or sedimentary rocks in a variety of geologic environments.
حقوق النشر © 2024.Artom كل الحقوق محفوظة.خريطة الموقع