Utilization of Pellet Fines in the Iron Ore Sintering Process
The sinter plant that converts the iron ore fines into a desirable blast furnace feed, offers an avenue for recycling wastes. One of the several wastes that are produced at an iron and steel plant is the undersized pellet fines, which cannot be directly used in iron making. The present study evaluated the influence of these pellet fines on the sintering …
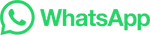