Comparison of sample properties and leaching
The use of HPGR instead of jaw crusher as the crushing method of ore before heap leaching has always been an effective method to improve leaching efficiency (Kodali et al., 2011; Yin et al., 2017
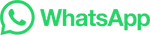
The use of HPGR instead of jaw crusher as the crushing method of ore before heap leaching has always been an effective method to improve leaching efficiency (Kodali et al., 2011; Yin et al., 2017
9 Jun 2022; Heap leaching is a method of spraying the ore heap with a leach solution to selectively leaching the useful components in the ore during the downward infiltration process, and recovering the useful components from the rich liquid flowing out of the bottom of the heap.
The design specifications were met (Table 1). The plant achieved of -6 mm crushing product with the target size of 80% of -4.55 mm at a capacity of 200 (±10%) Mg/h. The product size for the best recovery, 3.35 mm, was measured between 63% and 68%. Secondary crushers achieved reduction ratio of 2–2.5 in average.
Heap Leaching. If higher recoveries and faster leach kinetics is important to you, HPGR should be a consideration for your heap leach flowsheet. The microcracking in HPGR product lends itself nicely to the heap leaching …
HPGR products can still be leached efficiently after agglomeration. Abstract. High-pressure grinding rolls (HPGR) technology is a valuable way to improve the …
Oxide ores are generally processed using hydrometallurgy. This process uses aqueous (water-based) solutions to extract and purify copper from copper oxide ores at ordinary temperatures, usually in three steps: heap leaching, solvent extraction, and electrowinning. Heap Leachingis the process of using percolating …See more on superfund.arizona.edu
WEBBased on the extensive experience of heap leaching operations, crushed ore agglomeration can be successfully considered and utilized as a pretreatment step for the …
The Nickel Matte Sulphate Leaching Process offers a proven processing method for various nickel containing raw materials. 's industry leading sulphate-based pressure leaching is the key to the process to guarantee high recoveries of nickel, cobalt and precious metals. Contact our sales experts.
heap are the main concerns in the kinetics of leaching. In. general, the kinetics of leaching includes particle reaction. + transport phenomena and reactor-level reaction +. transport phenomena ...
Sustainable solution. Energy and resource efficient leaching process and proprietary equipment. The leaching process. Leaching is the liberation of metals from ores by chemical dissolution, and it forms the basis of most …
One. Improve the process layout of the bag filter and arrange the filter of the crusher according to the direction of the belt conveyor. The standard dust hopper of the bag filter is changed into a double dust hopper structure. We cancel one screw conveyor and raise the bag dust collector, which is beneficial to the arrangement of air inlet ...
Silver ore processing technology is used for recovering silver and associated metal minerals. Silver-bearing ores have two types: silver-gold ores and lead-zinc-copper associated ores. The flotation & …
Gravity Recovery & Au/Ag Leaching - CCD Merrill Crowe Plant & Refinery: This complete hydrometallurgical process plant is for recovering precious metal from oxide or very low sulphide ore deposits containing silver …
However, during the leaching process, due to the physical, chemical and biologic reactions in ore, granular media under the role of solution could affect permeability. ... the first being the comminution of the ore using the HPGR and cone crusher and the second part were leaching in the eight leach reactors. 2.1. Ore preparation.
The Leaching process is a universal process – Water will leach the components of any material it comes in contact with, from its surface or the interior of the material (based on the porous nature of the material). Using this process, the ore of metal can be concentrated by causing a chemical reaction with a reagent which would lead to the ...
The placer or rocks mined from underground which contains gold is called ore. The gold mining process involves crushing the ore into sand and dust to liberate and recover the gold. What's leftover is called tailings. Ballarat Gold Mine uses its robust management and monitoring processes to make sure its produced gold tailings comply …
Once leaching process has been completed, the solution is filtrated under vacuum, following the Buchner method, and several washes are followed. Finally, the solid phase is dried overnight at 120 °C, pulverized and subjected to X-ray fluorescence spectroscopy (XRF), in order to determine the after leaching PGMs' concentrations. ...
Based on analysis of the test results, we work closely with in-house experts to develop robust, efficient, and cost-effective process plant flowsheets for all stages of your extraction process. Our expertise includes comminution (crushing and grinding), flotation, leaching and dewatering. Services. Design and evaluation of flowsheets for ...
Contribute to naicha22/2022 development by creating an account on GitHub.
Diamonds processing flow. Stage 1 – Crushing. Once the diamond-bearing ore and gravel are collected, it is transported to a primary crusher. The primary crusher is responsible for reducing the size of the ore into smaller, more manageable pieces or chucks measuring no larger than 150mm.
Abstract. Based on the extensive experience of heap leaching operations, crushed ore agglomeration can be successfully considered and utilized as a pretreatment step for the heap leaching of ores containing significant amounts of fines and clay minerals. The drum agglomeration is considered as a pretreatment step for the heap leaching of …
Heap leaching (HL) is a flexible and economic gold ore processing method used to extract gold from low-grade gold ores. In this process, ore is firstly crushed to fine particles. By spraying leaching solution to the large piles, the gold-containing solution is leached. Then used the gold processing method of carbon adsorption, zinc powder displacement device …
The leaching rates of Li, Fe, Al and Ti were 99.24%, 0.10%, 2.07% and 0.03%, respectively. According to Fig. 3, aluminum was first dissolved by acid in the form of an elementary substance during the oxidative leaching process. With the consumption of acid, the pH value increases, and aluminum enters the residue phase in the form of …
Leaching is a mass transfer process which takes place through the extraction of a substance from a solid material that has come into contact with the liquid. Leaching is the normal mechanism by which water-soluble compounds from soil or waste are washed out. Such leached-out contaminants affect surface and subsurface water contamination.
The Pineer gold cyanide leaching process enables sustainable and cost-effective gold recovery >90%. Comes from one supplier, responsible for the whole package. Provides mechanical and performance guarantees for the entire plant unit, with clear battery limits for engineering and implementation. Provides optimal process performance with …
The present study aims to evaluate the feasibility of dissolving the low-grade copper oxide deposit, rejected of the jaw crusher, in sulfuric acid solutions and develop …
To solve the problems of the long development period, low mass transfer efficiency and high impurity content in the in-situ leaching process of weathered crust elution-deposited rare earth ores (WCE-DREO), cationic hydroxyethyl cellulose (PQ-10) was composited with conventional leaching agent ammonium sulfate ((NH 4) 2 SO 4) to form …
In this study, the reject fraction of the jaw crusher, located in the rst part of the crushing circuit, is used as a consider-able stock in copper tank-leaching plant. High market …
This is done by contacting the carbon with a solution of sodium cyanide. (0.1 to 2% by mass) and sodium hydroxide (0.1 to 2% by mass) at high temperatures (90–120°C). This results in the reversal of the adsorption process with most of the gold desorbing from the carbon back into solution.
Oversize from the double-deck screen feeds through the secondary crusher, a 1.7 m (5½ ft) Standard Cone Crusher equipped with coarse liners set at 25.4 mm (1 in) opening, and then over a 1.83 m by 3.66 m single deck Allis-Chalmers vibrating screen also utilizing a 12.7 mm square screen cloth and into the tertiary crusher.
Primary crushing operations takes boulder size feeds (20 to 100 inches) and reduces the material to secondary crusher feed size (1 to 20 inches) or mill feed size (0.5 to 3 …
حقوق النشر © 2024.Artom كل الحقوق محفوظة.خريطة الموقع