Crushing and Screening Plant in dubai | Mining & Quarry …
Philippines 150TPH Riverstone Crushing Plant; Indonesia 180 tph Iron Ore crushing plant; How Much VSI Sand Crusher; How much the ball mill and capacity? Four in one type mobile crusher used in Kenya; Limestone TGM130X Grinding mill in Egypt; Saudi Arabia Dolomite Grinding Mill; Categories. Beneficiation Plant; Crushing Plant; …
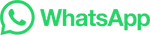