Grinding Mills and Pulverizers Selection Guide: Types, …
Important specifications when selecting grinding mills and pulverizers include, The size of the mill can range from pilot/lab to production, e.g., 3.5 to 1600 cu. ft. Feed size, material, and hardness of feed must be considered. Output size …
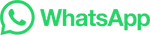