How Cement Is Made
Cement is so fine that 1 pound of cement contains 150 billion grains. The cement is now ready for transport to ready-mix concrete companies to be used in a variety of construction projects. Although the dry process is the most modern and popular way to manufacture cement, some kilns in the United States use a wet process. ...
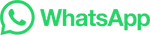