Planetary Ball Mill PM 400
Download. The PM 400 is a robust floor model with 4 grinding stations and accepts grinding jars with a nominal volume from 12 ml to 500 ml. It processes up to 8 samples simultaneously which results in a high …
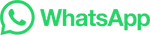
Download. The PM 400 is a robust floor model with 4 grinding stations and accepts grinding jars with a nominal volume from 12 ml to 500 ml. It processes up to 8 samples simultaneously which results in a high …
Run-in: The balls were submitted to 30 h of wear in the pilot-plant ball mill, grinding coarse quartz sand (0.3–2.5 mm). This step provided the removal of a layer of about 100 μm, thus removing oxide scales and other defects from the surface. (2) Grinding periods of 10 h each, up to 70 h total grinding time.
If you believe the entry ball size sets the initial point on ball population and exit size is fixed, since the ball wear is near linear, in some camps, this raises the P80 = can only result in grinding larger rock. ... Ball mill liner efficiency based on liner geometry and its influence on kW-hours/ton, total tons/life cycle, and P80 transfer ...
About Us. Wuxi Orient Anti-wear Co., Ltd. We are a specialized manufacturer of wear and heat resistant castings. Our main products are Mill Liners for Ball Mills,SAG Mills,AG Mills,Crusher Wear Parts and Grinding Media. 1.The failure of ball mill liner is basically divided into three forms Fracture failure of ball mill liner: Ball mill liner in the production …
5. The size of the ball mill is large, and it is necessary to carry out lifting work during the process of replacing the ball mill liner. The hoisting ball mill liner is the responsibility of the hoist. The lifting process requires attention to the operation of the wire rope and the hook. 6.
To this end, a laboratory-scale ball mill was used to evaluate the variation of wear process of the lifter in different milling conditions of mill speed, ball filling, grinding …
Traditionally, mill media wear rate is evaluated by measuring the media level in the mill, or by removing media charge and weighing it after a certain number of hours. As mentioned above, the mill was stopped after 24 h (one cycle) with a total of 24 cycles for each ceramic ball type. Grinding tests were carried out for 24 days (576 h) and ...
The influence of the ratio of mill size on the rate of wear ∅4(d/D) can more conveniently be written in the form ∅4(D/d), and in Fig. 8.7 are plotted the data of Coghill and Devaney and Gross, relating to the wear of balls when the charge consists of balls of uniform size, and of McLeod, relating to the wear of balls of size d in a charge ...
The energy con sumption for spherical balls was 3.6 Kw after grinding for 420 minutes, producing a 45µm. residue of 4.37% whilst that of cylpebs was 2.6kW after grinding for 295 minutes producin ...
Wear of Grinding Balls with a Size Distribution in Dry and Wet Tumbling Mills. Naoya Kotake H. Takeuchi Y. Kanda. Engineering, Materials Science. 2008. The wear generated in grinding balls having a ball size distribution in a tumbling mill was investigated using a laboratory-scale mill for both dry and wet grinding.
Cement grinding with our highly efficient ball mill. An inefficient ball mill is a major expense and could even cost you product quality. The best ball mills enable you to achieve the desired fineness quickly and efficiently, with minimum energy expenditure and low maintenance. With more than 4000 references worldwide, the FL ball mill is ...
How to install a ball mill, how to operate a ball mill, how to maintenance a ball mill. Ball mill installation, operation, maintenance, wearing parts list. +86-371-60305814
Kehrs Mill Veterinary Care, Ballwin, MO. 201 likes. Newly opened full service dog and veterinary clinic in Ballwin, MO
proud to say that the ball mill feed spout solution has significantly less embedded CO. 2. emissions that previously supplied cast alternatives. Ball mill feed spouts experience constant wear and need to be changed periodically to allow ongoing operation. 's design offers a holistic solution to common chute problems. Grinding services
Proper sizing of ball mill output is critical to ensure efficient processing of your minerals. Tri-Braze, with its through hardened interior, ensures the edge retention and hole …
CERAMIC LINED BALL MILL. Ball Mills can be supplied with either ceramic or rubber linings for wet or dry grinding, for continuous or batch type operation, in sizes from 15″ x 21″ to 8′ x 12′. High density ceramic linings of uniform hardness male possible thinner linings and greater and more effective grinding volume.
A ball mill consists of various components that work together to facilitate grinding operations. The key parts include the following: Mill Shell: The cylindrical shell provides a protective and structural enclosure for the mill. It is often made of steel and lined with wear-resistant materials to prolong its lifespan.
Performance Of Ball Mill: 1. The new ball milling machine can save power of motor of 30-40%, lubricating oil 70%, cooling water 90%, and the comprehensive saved energy is over 40%. 2. The headstock of the ball …
A ball mill is a type of grinder used to grind or blend materials for use in mineral dressing processes, paints, pyrotechnics, ceramics, cement, etc. It works on the …
The ball mill abrasion test (BMAT) promises to offer accurate prediction of relative service lives of wear-resistant alloys for liners and grinding media in mineral grinding environments. Relative alloy performance depends strongly on the abrasive minerals present. Towards a greater understanding of factors controlling relative …
The present literature review explores the energy-efficient ultrafine grinding of particles using stirred mills. The review provides an overview of the different techniques for size reduction and the impact of energy requirements on the choice of stirred mills. It also discusses the factors, including the design, operating parameters, and feed material …
A ball mill consists of a hollow cylindrical shell that rotates about its axis. It is partially filled with balls that can be made in chrome steel, stainless steel, rubber or ceramic. The inner part of the shell is usually lined with an abrasion-resistant material such as manganese steel or rubber. For many years, Hardox® steel has been used ...
Best Veterinarians in Ball Ground, GA 30107 - Ball Ground Animal Hospital, Sunrise Veterinary Hospital, Persimmon Creek Animal Hospital, Paw Project of Georgia, Acres Mill Veterinary Clinic, Project Catsnip, Destination Pet of Woodstock, Williamson Debbie DVM, Sweet Dreams In-Home Pet Euthanasia, Heartstrings Veterinary Hospice, In-Home …
Ball Mill Liner Manufacturer. Qiming Machinery is one of the largest ball mill liner manufacturers in China. Qiming Machinery's ball mill liners are tailor-made and developed in close collaboration with our customers. Being the pioneer, Qiming Machinery ball mill liners are designed and produced based on the world's largest bank of know-how ...
wear china vet ball mill. ZHANGGU.Co.,Ltd. Shandong Zhangqiu Blower Co., Ltd. is a national key fluid machinery manufacturer with 50 years of fluid machinery design, manufacturing technology and experience. The company has established two Sino-Japanese joint ventures and set up branches in the United States, becoming the first …
The theory of the calculation of the size distribution of the equilibrium mixture of balls in a ball mill is developed. The differential equation is solved for wear laws of the form wear rate per ball ∝ r 2 + Δ where r is ball radius. Δ = 0 gives the Bond wear law and Δ = 1 gives the Davis wear law. Methods of determining Δ are illustrated.
feed hopper and feed screw cylinder. Check the wear part of the. discharge screen and discharge hood of the discharge part, and repair. it regularly. 2. The rotating part of the …
The Current Wear of the Cylinder Liner Structure. The data of this research comes from the SAG mill (8.53 m × 3.96 m) used in the SABC grinding process of a concentrator in Anhui, China. This SAG mill adopts two L-shaped high and low liners arranged back to back, as shown in Figure 1. Figure 1.
The experimental results showed that the Abbott-Firestone curve can evaluate the lifter surface topography. The wear rate of the lifter specimen is increased first and then decreased with mill speed and grinding media size. Increasing ball filling will increase the wear rate, and the grinding media shape of ball has a maximum wear rate.
Mill Liner Profiler Tool -Track Liner Wear Pattern. Here is a home-made tool to measure or obtain a fingerprint of your SAG and Ball Mill Liner wear pattern/profile. Each time you shut down, get a profile and build a wear-life over time database to better predict your next reline job or monitor improvements to your liner design.
حقوق النشر © 2024.Artom كل الحقوق محفوظة.خريطة الموقع