Types of Rock Crushers | Quarry Crushing …
Typically, the minimum setting on most primary crushers will be about 4 to 6 inches, as noted above. Compression-style jaw, cone, impact crushers, and gyratory crushers are most often appropriate as primary crushing …
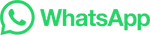