® LT106™ mobile jaw crusher
® LT106™ mobile jaw crusher, or mobile jaw crushing plant as it is also called, is often used as a primary crusher in a multistage crushing process or as a stand-alone unit. It is ideal for medium-sized aggregates production, as well as recycling demolition waste such as crushing concrete, which can be re-used as base material for ...
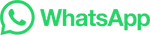